Mastering Lapidary Grinding: Techniques and Insights
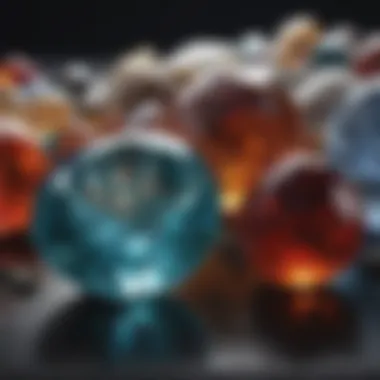
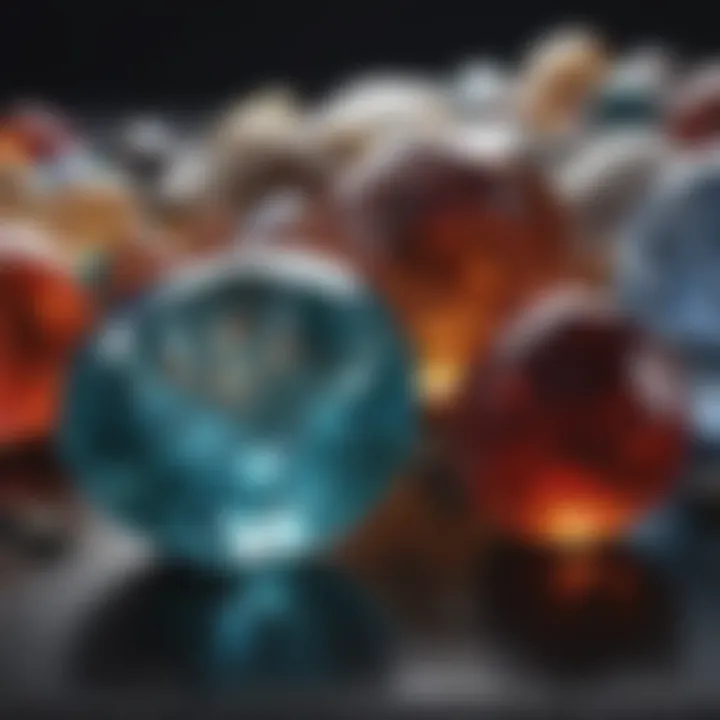
Overview of the Topic
Lapidary grinding is a delicate dance between art and science, transforming rough stones into stunning gems. It’s not simply about cutting away at rock; there's a depth of knowledge, skills, and tools involved. Let's take a moment to unpack what we mean by lapidary grinding, along with its historical significance.
Definition of Key Terms
At its core, lapidary grinding refers to the process of shaping and polishing gemstones using various techniques and tools. The term "lapidary" itself comes from the Latin word lapidarius, which means "of stone". The main goal of this craft is to bring out the natural beauty of the stones, making them suitable for various uses, particularly jewelry.
Some key terms to familiarize ourselves with include:
- Grit: The size of the abrasive particles on grinding wheels, which ranges from coarse to fine.
- Polishing: The final step that enhances a stone’s luster and brilliance through finer abrasives.
- Cabochon: A gemstone that has been shaped and polished, but not faceted; typically rounded for aesthetic appeal.
Historical Significance
Lapidary work has ancient roots, tracing back thousands of years. From the early Egyptians who used simple tools to carve gemstones for amulets and burial decorations, to the skilled artisans of the Renaissance who crafted fine jewelry, lapidary grinding has always held cultural importance. The craft served not only as a means of artistic expression, but also held religious and economic significance in various societies.
In the modern age, the revival of lapidary techniques has caught the eye of both collectors and hobbyists. This resurgence speaks not just to a love for beautiful items, but also to a desire for mastery in a craft that connects us to history.
Techniques in Lapidary Grinding
Grinders and polishers are an indispensable part of the lapidary artist's toolkit. Understanding the specifics of each technique can vastly influence the final product. Various techniques vary not just by the use of machines but also by the styles and finishes desired. Here’s a glimpse:
- Flat Lapping: This technique involves passing the stone against a flat surface, ideal for creating even surfaces on cabochons.
- Rotary Grinding: Utilizing a rotating disk or wheel, this method is best for achieving intricate details and shapes.
- Sanding: A crucial step after grinding, sanding smoothens rough edges and prepares surfaces for polishing.
- Polishing: Using fine abrasives, this method enhances the stone's shine, making it truly captivating.
These methods lay down the groundwork but merging them with creativity turns an ordinary piece into something extraordinary. Lapidary grinding ain't just a process; it’s a skill that takes time, patience, and passion to master.
"It's not about the stone itself, but the journey you take to unveil its true character."
By diving into lapidary grinding, enthusiasts not only hone their technical abilities but also connect with a timeless tradition that speaks to the very essence of craftsmanship.
Intro to Lapidary Grinding
Lapidary grinding represents a fascinating intersection between art and science, capturing the attention of gem enthusiasts and aspiring collectors alike. Understanding the intricate processes behind this craft is essential for anyone looking to delve deeper into the world of gemstones. Through lapidary grinding, rough stones are meticulously transformed into polished works of art, revealing their hidden beauty and intrinsic value. This section aims to unpack the fundamental aspects of lapidary work while providing a window into its historical evolution, offering invaluable insights for both hobbyists and professionals.
Understanding Lapidary Work
To grasp the significance of lapidary grinding, one must first understand what lapidary work encompasses. This craft is not merely about cutting and polishing stones; it is about harnessing an ancient technique that has withstood the test of time. Lapidaries utilize various tools and methods to shape raw stones into stunning pieces, paying homage to centuries of tradition while incorporating modern advancements.
Experts often say that every stone tells a story. Through careful grinding and shaping, lapidaries can accentuate each stone's unique characteristics. The nuances in color, texture, and inclusions come to life, allowing collectors to appreciate the natural beauty in each gem. This tactile experience fosters a connection between the lapidary and the stone, creating art that resonates both visually and emotionally.
The Evolution of Lapidary Techniques
Over the centuries, lapidary techniques have undergone significant transformations, evolving alongside technological advancements and cultural shifts. From the earliest methods used in ancient civilizations to the sophisticated tools available today, the craft has adapted while remaining true to its roots.
In the past, lapidaries relied heavily on handheld tools and rudimentary machinery, often using materials available in their surroundings. Hand polishing stones on leather with abrasive powders was common practice, and each step was labor-intensive.
Today, the landscape has changed dramatically. Innovations such as diamond-tipped tools, powered grinders, and specialized polishing compounds have allowed lapidaries to achieve remarkable precision and efficiency. This evolution not only enhances the quality of the finished product but also expands the possibilities for creativity in design.
The craft continues to thrive, attracting new generations drawn by the allure of transforming unassuming stones into exquisite gems.
"In every gem is a masterpiece waiting to be revealed." Through exploration and understanding of past and present techniques, collectors can appreciate the artistry involved in lapidary work while recognizing the continuous journey of its advancement. Whether you are just starting or looking to refine your skills, acknowledging this evolution is key to mastering the art of lapidary grinding.
Tools and Materials Used in Lapidary Grinding
In the world of lapidary grinding, the choice of tools and materials plays a pivotal role in shaping the outcome of the work. Whether a seasoned pro or a weekend hobbyist, having the right gear at your fingertips not only enhances efficiency but also maximizes the quality of the finished gem. Tools and materials are not just accessories; they are the backbone of the lapidary process. Knowing what works best for different stones and techniques can set apart a polished gemstone from a mediocre one.
Essential Tools for Lapidary Grinding
Grinding Wheels
Grinding wheels are essential in the lapidary process as they remove material from the stone. These wheels come in various grits, from coarse to fine. The key characteristic of grinding wheels is their abrasive surface, which can drastically alter the shape and size of the stone and is known for its longevity. Generally speaking, diamond grinding wheels are a popular choice because they can cut through even the toughest materials like quartz or jade with ease.
One unique feature of diamond grinding wheels is that they offer exceptional precision while being heat-resistant, crucial for maintaining the integrity of the gem. However, a drawback can be their cost, which is significantly higher than traditional wheels. Yet, when you’re working with valuable stones, investing in a good diamond wheel can be worth every penny.
Polishing Pads
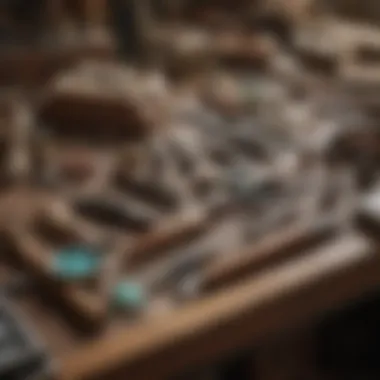
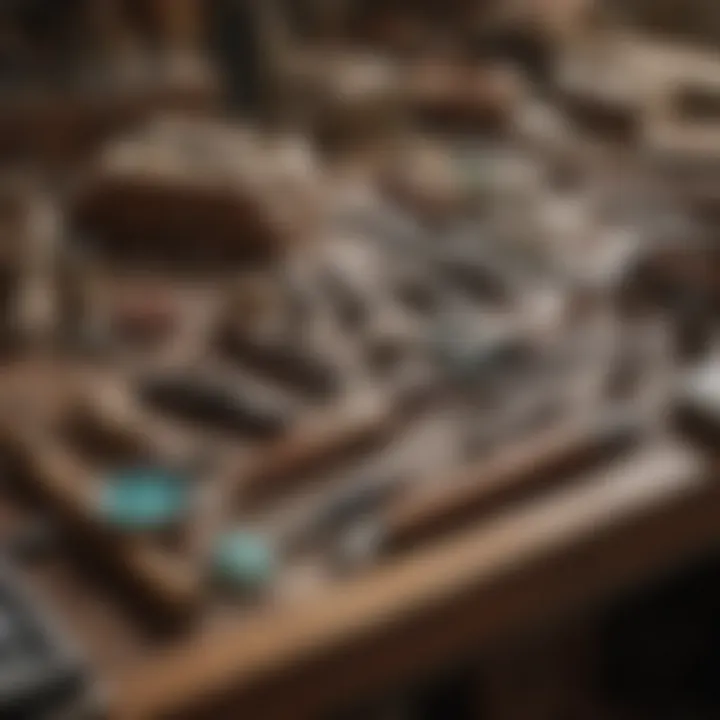
Polishing pads come into play after the rough grinding is done, assisting in achieving that gleaming finish that turned heads. The primary characteristic of a polishing pad is its soft texture, typically made of natural or synthetic materials designed to conform to the shape of the stone. They provide a smooth finish, ensuring that scratches from previous grinding steps are absent in the final piece, which is critical for market value.
What makes polishing pads unique is their ability to use different compounds like cerium oxide to further enhance shine. The main advantage of using these pads is that they can provide a flawless polish without altering the stone's shape. However, they can wear out quicker than grinding wheels, necessitating timely replacements to maintain consistent quality.
Water Supply Systems
Water supply systems are often overlooked but are vital in the lapidary grinding process. These systems help to cool the stone and the tool while minimizing dust, preventing both from creating an unsafe work environment. The main feature of a water supply system is its ability to keep everything hydrated, which, in turn, reduces the risk of overheating when grinding.
A unique advantage of having a reliable water supply is that it aids in oleasing the stone, allowing for a better grinding finish. However, finding the balance in water flow can be a challenge; too much water may lead to slippage, while too little can create a dusty mess, complicating the process and potentially damaging the stone. Therefore, care should be taken to set up an effective system that fits one's specific working habits.
Types of Stones and Their Properties
Understanding the types of stones and their respective properties serves as a foundation for effective lapidary grinding. Each stone presents its own challenges and opportunities, impacting everything from the choice of tools to the techniques employed.
Soft vs. Hard Stones
In the realm of lapidary work, differentiating between soft and hard stones is crucial. Soft stones, like alabaster or calcite, require less aggressive tools and can be shaped relatively quickly. Their key characteristic is the ease with which they can be worked, making them a go-to for beginners.
Conversely, hard stones, such as sapphire or diamond, demand specialized equipment and techniques. While they offer exceptional brilliance and durability, their toughness can lead to frustration without the right tools. The unique feature of hard stones lies in their ability to maintain a perfect polish for an extended period. Yet, the downside is that they significantly test the skills and patience of any lapidary artist.
Common Gemstones in Lapidary Work
When it comes to lapidary work, certain gemstones stand out due to their popularity and appeal. Stones such as amethyst, opal, and turquoise are commonly used, each carrying its distinct allure. The key characteristic of these gemstones is their varied colors and patterns, making each piece unique.
What sets these common stones apart is their cultural significance and potential market demand. While they are more accessible for novices, challenging aspects include their sensitivity to heat and pressure, which demands careful handling throughout the grinding and polishing processes. Ultimately, the allure of these gemstones lies not just in their beauty, but also in the satisfaction derived from transforming them into polished works of art.
Techniques in Lapidary Grinding
Lapidary grinding is not merely a craft; it is a harmonious blend of art and science. The techniques employed in this craft can significantly affect the final product's quality and aesthetic appeal. Understanding the nuances of these techniques allows for better control over the grinding process. Each method has its unique contributions, advantages, and disadvantages, making it crucial for hobbyists and professionals alike to master these skills.
Different Grinding Techniques
Flat Grinding
Flat grinding stands as one of the most fundamental techniques in lapidary work. This method primarily involves creating a level, flat surface on the stone. The process is often regarded as an essential first step in shaping gems before any detail work is done. It provides a sturdy foundation, allowing lapidaries to assess the stone's potential.
One key characteristic of flat grinding is its straightforwardness. It allows for precision in achieving even surfaces, which is beneficial when preparing stones for further shaping. The use of a flat wheel facilitates uniform removal of material, minimizing the risk of uneven wear on the stone. However, the technique requires a gentle touch because excessive pressure can lead to larger scratches or gouges on the surface.
A unique feature of flat grinding is that it is often combined with water to maintain a cool temperature and minimize dust. This cooling effect not only protects the stone but also extends the life of the grinding wheels. The disadvantage, however, is that it can lead to a messier workspace, so adaptations might be needed to manage water flow effectively.
Bevel Grinding
Bevel grinding takes a step forward from flat grinding by angled surfaces. This technique is particularly useful for stones that require a shaped edge, such as pendants or rings. The defining element of bevel grinding is the angular surface results, which add a different dimension of style that flat grinding alone cannot achieve.
The angle applied can be adjusted to fit specific design criteria, making bevel grinding a favorite among those looking to incorporate intricate details. It offers a unique blend of functional and aesthetic appeal. One major advantage is that it enhances the light interaction with the stone, creating brilliant reflections that can elevate its overall appearance.
Despite its benefits, bevel grinding does come with challenges. It can be harder to master than flat grinding since improper angles might lead to an unbalanced look. Furthermore, this method requires more careful planning when compared to flat grinding, making it slightly less accessible to beginners.
Cabochon Cutting
Cabochon cutting centers on creating stones with rounded profiles often used in jewelry making. It serves as a beautiful alternative to faceted gems, offering a softer and more organic feel. The end result of cabochon cutting showcases the stone’s natural color and patterns, making it a favored choice amongst collectors who appreciate unique pieces.
What makes cabochon cutting particularly interesting is its focus on the stone's natural beauty, showcasing patterns and translucence in a way that other techniques may overlook. Unlike the precision required in faceted stones, cabochon cutting emphasizes a smoother, curved surface, which feels more approachable for many lapidary enthusiasts.
The downside, however, lies in its learning curve. Achieving the perfect dome shape requires practice, and the lack of sharp edges makes it less forgiving for mistakes compared to grinding techniques that allow for more harsh corrections. Thus, while cabochon cutting is rewarding, it challenges the grinder to develop a steady hand and an eye for design.
Polishing Techniques for a High Shine

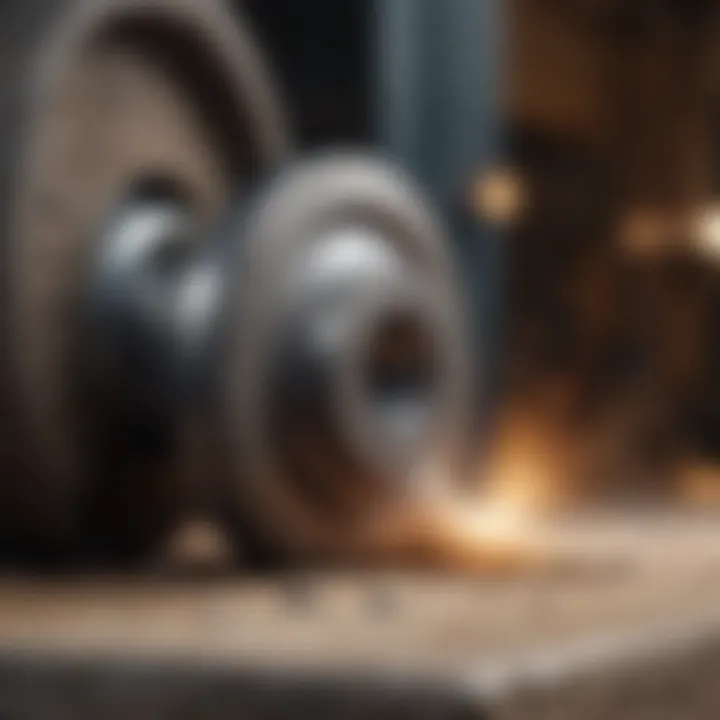
Achieving a high shine in lapidary work entails various polishing methods. The finishing touch can make a world of difference, as a well-polished stone not only looks more appealing but also feels appealing to the touch. Each polishing technique has its unique aspects, and understanding them can further enhance the final product.
Use of Cerium Oxide
Cerium oxide serves as a powerful polishing compound mainly preferred for quartz and other hard stones. It creates a brilliant finish by enhancing the stone's natural luster without compromising its integrity. Its fine particle size allows for a smooth application, which is ideal for achieving that perfect high shine.
The use of cerium oxide stands out due to its versatility. It works exceptionally well on various stone types, providing beautiful results, whether it's an ordinary piece of quartz or a more exotic stone. However, it also presents some challenges; cerium oxide can be a bit tricky to work with, as the incorrect mixture can result in a less effective polish.
Diamond Polishing Compound
Diamond polishing compounds are often touted for their unmatched effectiveness in providing a superior shine. This method utilizes tiny diamond particles to polish stones, making it suitable for a broad range of materials. Due to the diamonds' hardness, this technique not only reduces polishing time but also gives an exceptional finish.
The significant advantage of diamond polishing is its efficiency; it can quickly remove scratches that may have been left from prior grinding techniques. However, the cost of diamond compounds can be a factor when budgeting for supplies, often making it less accessible for casual lapidary enthusiasts.
Buffing Techniques
Buffing techniques elegantly wrap up the polishing process. Buffing wheels, typically made from soft materials, apply a light pressure to the stone, creating a reflective surface. This method is highly effective for maintaining the polish already established through previous techniques, adding an additional layer of shine.
The beauty of buffing lies in its simplicity. With the right setup, it can finalize pieces quickly, making it necessary for professional lapidaries often short on time. Yet, over-buffing can lead to an unintended haze on the stone's surface. Thus, care must be taken to assess how much buffing is needed to preserve clarity and brilliance.
To ensure the best results with each technique, it's vital to respect the material you are working with, whether through safe practices or selecting the proper tools to support your creativity.
Understanding these techniques in lapidary grinding allows for a more structured approach to crafting beautiful gemstones. The combination of these methods can ultimately lead to extraordinary results, catering well to the tastes of collectors and creators alike.
Safety Considerations in Lapidary Work
Safety in lapidary work is not just a consideration; it's a fundamental element that ensures both the craftsman and the quality of the gemstones they shape are protected. The process of grinding stones, while rewarding, comes with its own set of risks. Understanding these risks and implementing appropriate safeguards can prevent injuries and maintain a productive working environment.
Personal Protective Equipment
Goggles and Face Shields
Using goggles and face shields is crucial in lapidary grinding to protect your eyes and face from flying debris. When grinding stones, even small chippings can become projectiles. Goggles specifically offer a snug fit and shield your eyes from dust, splinters, and any other projectiles that might arise during the grinding process. The clarity provided by high-quality lenses ensures visibility without distortion. On the other hand, face shields provide additional protection, particularly for the lower face, and are often used in conjunction with goggles for full coverage. Reliability and comfort are key traits that make these protective gears essential, especially for those who spend hours at their workstations.
Respirators
Respirators are vital when working with stones that can produce harmful dust particles. Breathing in these particles can lead to respiratory issues over time, particularly with materials like quartz or certain harder stones. A good quality respirator not only filters out dust but also reduces the inhalation of silicate particles. Many hobbyists appreciate the comfort of multi-layered filters, which allow for easier breathing while still offering protection. The unique construction of respirators, equipped with replaceable filters, means you can maintain a high level of safety without compromising comfort or risking reduced visibility while working.
Gloves
Gloves serve as your first line of defense against cuts and abrasions that can occur when handling rough stones and working near sharp tools. Good lapidary gloves are made from durable materials that also allow for dexterity while handling smaller gemstones. Many choose gloves that have reinforced areas for added protection without sacrificing the ability to maintain grip and sensitivity. While they provide excellent protection, it’s important to select gloves that fit properly so they won't get caught on moving parts of machinery, which presents a risk of injury.
Workshop Safety Practices
Proper Ventilation
Proper ventilation in the workshop is essential. It helps in clearing out dust particles and harmful vapors generated by grinding and cutting processes. A well-ventilated space minimizes the risk of respiratory problems and creates a more comfortable working environment. Installing exhaust fans or opening windows can help create air circulation. Additionally, this practice prevents the buildup of dust which can accumulate and pose fire hazards. Investing in a good ventilation system is often seen as beneficial for any serious lapidary artist, particularly those who carry on with larger projects.
Managing Dust and Debris
Managing dust and debris should be a priority in any lapidary workshop. Not only is dust a respiratory concern, but it can also settle on tools and equipment, affecting their performance. Regularly cleaning surfaces and employing water during grinding can significantly reduce airborne dust. Furthermore, using dust collectors or vacuum systems can provide an effective strategy to maintain a clean working area. Keeping the workspace tidy also aids in efficiency, allowing for more fluid motion throughout the grinding process.
Emergency Preparedness
Having a plan in place for potential emergencies is crucial. This includes knowing the location of first aid kits, fire extinguishers, and having an exit strategy in case of accidents. Training for emergencies is often overlooked but can save crucial time during an incident. Many craftsmen opt for regular safety drills to familiarize themselves with their equipment and emergency procedures. Being prepared fosters confidence and contributes to a more focused work environment.
"In art, as in life, prevention is better than a cure; prioritize safety from the start."
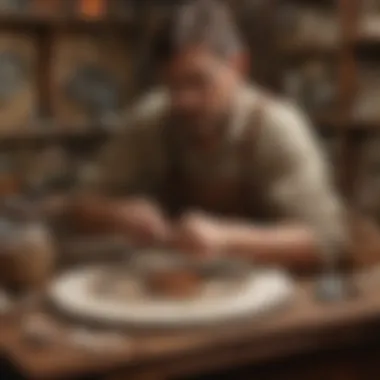
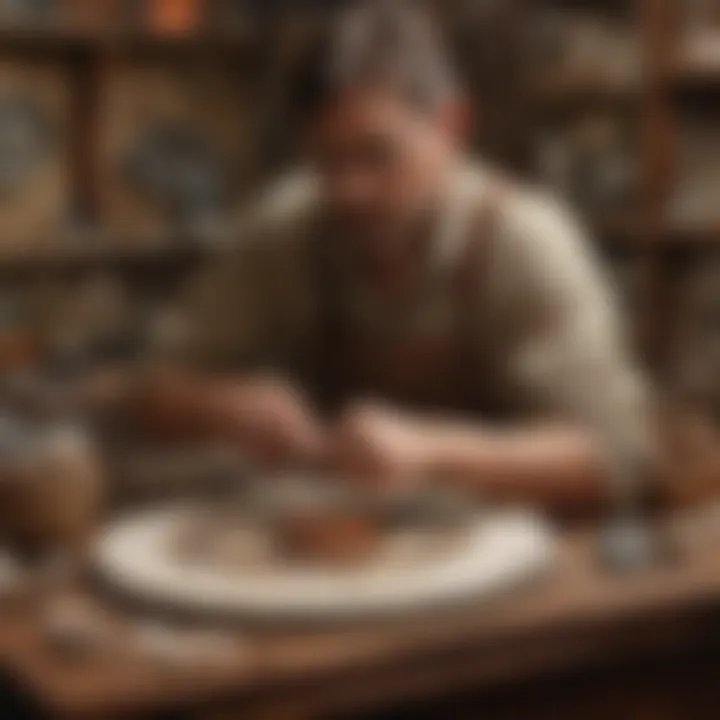
The Influence of Lapidary Grinding in Collectibles
Lapidary grinding is not merely a method of shaping stones; it significantly influences the allure and value of gemstones within the collectibles market. The meticulous process of grinding turns rough, uncut stones into breathtaking treasures that can define or enhance a collector's portfolio. This section sheds light on how this transformative artistry affects both the aesthetic appeal and market dynamics of gemstones.
Impact on Gem Value and Market
The Role of Craftsmanship
Craftsmanship is the backbone of lapidary grinding. A subtle yet powerful facet in the realm of gemstones, craftsmanship influences not just the physical attributes of a gem but its perceived value as well. It embodies the skills, precision, and artistic vision that a lapidarist pours into their work, often making or breaking the final product.
A well-crafted stone can whimsicality draw the eye and fetch a price higher than its less finely honed counterparts. Collateral to craftsmanship is attention to detail; the ability to notice the stone's unique characteristics determines how well the final piece resonates with potential buyers. Another key point is that craftsmanship can elevate the gem beyond mere aesthetics, infusing it with a narrative that increases desirability among collectors.
On the downside, exceptional craftsmanship requires time and patience, sometimes leading to higher costs that can deter entry-level collectors. However, for the seasoned enthusiast or investor, the investment in quality often pays off.
Market Trends in Lapidary Collectibles
Understanding market trends in lapidary collectibles is crucial for any collector looking to navigate the subtle waves of the gemstone economy. The demand for specific types of stones can fluctuate based on various factors, including trends in fashion, advancements in technology, and shifts in consumer values toward ethical sourcing and sustainability.
Currently, there is a growing market for unique and original pieces that tell a story, pushing pieces polished by hand—where the imperfections of human artistry might enhance the again desired character of the stone. So, taking those market trends into consideration can be beneficial for both new and experienced collectors. Gems that once appeared commonplace might suddenly gain traction, transforming a collector's findings into unexpectedly valuable assets.
This dynamic nature can create opportunities but also requires a touch of discernment from collectors eager to capitalize on their investments. Despite these advantages, being attuned to market trends does come with its challenges, as what is in vogue today might lose its shine tomorrow.
Lapidary Grinding for Personal Collections
Customization and Personalization
Customization and personalization are essential aspects of lapidary grinding that resonate deeply with collectors. When a collector chooses to grind or polish a gemstone according to their preferences, they engage in a dialogue with the stone itself. This intimate interaction can shape the piece into something personal, reflecting distinct tastes and aspirations.
The allure of creating a unique piece can often be more rewarding than purchasing something mass-produced. Personalization breathes life into the stone, whether it’s selecting a specific cut, adding unique engravings, or choosing a finish that sings to the soul of the collector. However, it’s worth noting that the journey of customizing a gem does involve experimentation, which can yield mixed outcomes without a good understanding of lapidary techniques.
Enhancing Aesthetic Appeal
The aesthetic appeal of a gemstone is more than surface-level beauty; it represents the intricate balance between shape, color, and clarity achieved through the grinding process. Enhanced aesthetics attract collectors not just for their physical attributes but for the emotional connections they foster.
Lapidary grinding techniques like beveling or cabochon cutting can make a significant difference in how light refracts through the gem, transforming even a commonplace stone into an eye-catching centerpiece. This effect can elevate the gemstone's status within one's collection, becoming a talking point or an heirloom worth passing down.
On the flip side, achieving such aesthetic appeal may require access to more sophisticated tools and a firm grasp of several techniques, something that can be daunting for newcomers. Nevertheless, the reward of beauty that can wow any viewer makes the effort undeniably worthwhile.
"Lapidary grinding transforms raw potential into refined artistry, crafting stories that stones carry into the hands of collectors."
The discourse around the influence of lapidary grinding within the collectibles landscape is rich and multifaceted. Through craftsmanship, market trends, and personal connections to custom pieces, gemstones find their treasured places not just on display, but also in the hearts and tales of avid collectors.
The End and Future Directions in Lapidary Grinding
As we wrap up our exploration of lapidary grinding, it's clear that the craft is not merely a set of techniques, but rather a fusion of art and science. It is the meticulous approach to transforming rough stones into stunning pieces that speak to both the heart and the eye of collectors. This section emphasizes the importance of ongoing innovation in techniques and tools, as well as predicting future trends that may shape the realm of lapidary work.
Continued Innovations in Techniques
Innovation in lapidary techniques has historically been a game-changer, evolving from rudimentary methods to advanced technology that enhances precision and efficiency. Consider the impact of CNC machines; these have revolutionized how stones are cut, allowing for intricate designs that were once impossible. Yet, despite the technological advances, the soul of lapidary—artistry combined with craftsmanship—remains essentially unchanged.
- Emerging Technologies: New grinding and polishing machines come on the market that use advanced ceramics and super abrasives. These materials not only increase the lifespan of equipment but also enhance performance.
- Personalization Techniques: As collectors lean towards more personalized pieces, the demand for unique shapes and custom finishes strengthens. Guided design software paired with advanced tools can help lapidists cater to bespoke requests.
- Sustainable Practices: As with many industries, environmentally friendly techniques are gaining traction. The rise of green abrasives and recycling of water used in grinding processes helps reduce lapidary's ecological footprint, addressing both consumer demand and ethical responsibilities.
These innovations offer not just practical benefits but also breathe new life into the traditional craft, paving the way for creativity that aligns with current societal values.
The Future of Lapidary Work for Collectors
The landscape of lapidary work is forever changing, molded by the preferences and values of collectors. The future holds exciting possibilities that promise to enrich the hobby and profession alike.
- Increased Accessibility: As lapidary tools and educational resources become more affordable and accessible, a new wave of enthusiasts will likely emerge. Local community workshops may feature classes that integrate traditional techniques with modern practices, encouraging hands-on experience and mentorship.
- Collectors' Role in Preservation: As interest in rare stones intensifies, collectors may play a pivotal role in preserving unique gem varieties by taking a more active stance in ethical sourcing. This ensures a steady supply of raw materials for lapidary artisans while also promoting awareness around issues such as mining practices and environmental sustainability.
- Digital Marketplaces: The rise of e-commerce and social media platforms allows collectors to share their passion and knowledge widely, increasing the visibility of unique creations and even turning hobbyists into small business owners. Vintage pieces can now find new homes around the globe with just a click.
In summary, the intersection of innovative techniques and evolving collector interests shapes not just the present but also the future of lapidary grinding. As the field moves forward, those engaged will find a rich tapestry of opportunities, encouraging both creativity and responsibility while maintaining the essence of the craft.
"True lapidary work is where art meets geology, and the possibilities are as endless as the stones themselves."
The journey of lapidary grinding continues to be a fascinating dance of tradition and progress, masterful techniques, and personal investment in stone. Embracing change while cherishing the roots of the craft ensures that this ancient art will continue to shine brightly in the world of collectibles.