Mastering the Dremel Lapidary Tool: Essential Insights
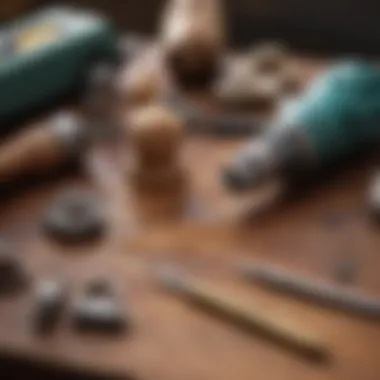
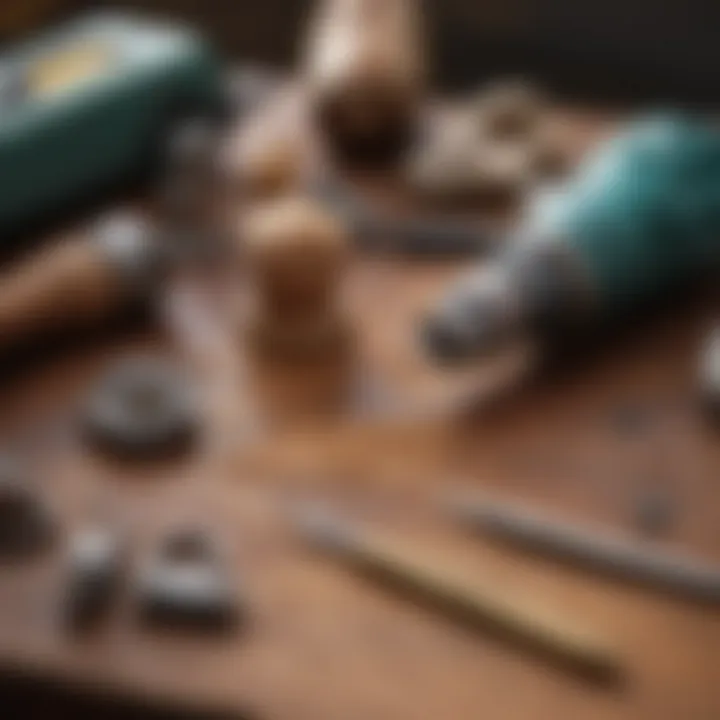
Intro
For hobbyists and seasoned rock collectors alike, the quest to create stunning lapidary pieces often hinges on having the right tools in hand. One standout in the realm of lapidary work is the Dremel tool, well-known for its versatility and precision. This article is here to shed light on the many ways you can utilize Dremel tools to craft and refine stones, offering a treasure trove of techniques and tips to elevate your skills.
With the rise of interest in DIY lapidary projects, it's crucial to understand not just how to use these tools, but their historical significance, best practices, and safety measures as well. Let’s embark on a journey that will not only clarify what lapidary work involves but also reveal the hidden potential of Dremel tools that can transform mundane stones into polished, eye-catching collectibles.
Prolusion to Dremel Tools in Lapidary
Dremel tools play a pivotal role in lapidary work, bridging the gap between amateur enthusiasts and seasoned artisans. Their versatility and precision are essential for anyone looking to shape, polish, and create exquisite works from stone and other materials. This introduction serves to highlight the significance of Dremel tools in lapidary tasks, emphasizing how they empower users to transform raw materials into art.
Lapidary is not merely a hobby but an art form that requires patience, practice, and the right tools. The Dremel tool, often regarded as a Swiss Army knife for lapidary work, offers a myriad of attachments and functionalities, making it a favored choice among collectors and creators alike. This section provides a concise overview of the foundational aspects of lapidary work and elaborates on how Dremel tools can elevate the crafting experience.
Overview of Lapidary Work
Lapidary work encompasses the cutting, shaping, and polishing of stones, minerals, and fossils into decorative items, jewelry, and collectibles. The essence of lapidary lies in the transformative journey—from a rough rock to a glimmering gem. It attracts a diverse community, including rock collectors, jewelers, and hobbyists.
The process usually involves several stages:
- Cutting: Using saws to slice through rough stones.
- Shaping: Grinding the stones to desired shapes and removing imperfections.
- Polishing: Achieving a smooth surface and enhancing the stone's natural luster.
In this context, the integration of Dremel tools offers a distinct advantage. They are compact, easy to handle, and can execute multiple functions, making them ideal for various levels of expertise in lapidary work.
Role of Dremel Tools
Dremel tools have revolutionized the lapidary landscape. Unlike traditional tools that may require more space and experience, Dremels are versatile and accessible. Their rotating bits and attachments can perform tasks ranging from cutting to intricate engraving, thus catering to a wide spectrum of lapidary techniques.
Some key roles of Dremel tools in lapidary work include:
- Precision Work: The ability to execute fine details, particularly useful for intricate designs.
- Ease of Use: Their lightweight nature and ergonomics make them manageable even during extended projects.
- Versatile Attachments: With a variety of bits, you can easily switch between tasks, whether it’s cutting, sanding, or polishing.
In essence, these tools are not just instruments; they are extensions of a lapidary artist’s vision, allowing creators to bring their ideas to life with efficiency and finesse.
"With the right Dremel tool in hand, the possibilities in lapidary work are endless, allowing anyone to sculpt their imaginations into tangible art."
Through this journey, this guide aims to unravel not just the hows but also the whys of employing Dremel tools in lapidary tasks. As we delve deeper, we will dissect the technology behind these tools and explore methodologies that seasoned lapidaries have mastered—ultimately offering readers a holistic understanding to hone their craft.
Understanding Dremel Tool Technology
The realm of lapidary work hinges on the tools used, with Dremel tools standing out prominently. Understanding how these tools operate is crucial for any lapidary enthusiast, as the right tool not only enhances the crafting experience but also influences the quality of the finished product. The intricacies of Dremel tool technology encompass motor power, speed control, and a variety of attachment options, each playing a key role in shaping stones and achieving desired results. This section aims to break down these elements, illustrating their importance and offering insights into practical applications for rock and fossil collectors.
Motor Power and Speed Control
One of the standout features of Dremel tools is their motor power and speed control capabilities. Potent motors provide the thrust necessary for effective cutting, grinding, and polishing of stones—essential shifts in speed can make a world of difference. By adjusting the speed setting, users can tackle different materials or specific tasks. For instance, while working with softer gemstones, a slower speed often prevents the material from overheating and fracturing.
Conversely, higher speeds can be better suited for tougher materials and intricate designs. This versatility allows lapidary artists to experiment and refine their technique according to the demands of their project. Imagine trying to polish a delicate piece of agate at too high a speed—one might end up damaging the stone beyond repair.
"The ability to finely control motor speed transforms a simple tool into a gateway for precision artistry."
When selecting a Dremel model, it's wise to consider the motor wattage as well. More powerful motors tend to sustain higher loads without straining, leading to smoother operation over time. Therefore, for those serious about lapidary work, investing in a Dremel tool with a robust motor can ensure reliability and effectiveness.
Attachment Options and Their Uses
Attachments are where the true magic happens with Dremel tools. Countless options are available, each meticulously designed for specific tasks. Some common attachments include grinding stones, polishing wheels, and cutting discs, with each one serving a distinct purpose, enabling users to go far beyond basic uses.
Grinding and Polishing Attachments
- Grinding Stones: Ideal for smoothing edges and shaping stones to a desired form. They come in various grits to suit rough jobs or detailed finishing work.
- Polishing Wheels: Essential for giving a glossy finish to your stones. Often made from soft fabric, these wheels can generate a beautiful shine when used correctly.
Cutting Discs
- Cutting Discs: These are a lapidary essential, especially when dealing with larger stones. Thin cutting discs are perfect for slicing through tough materials without excessive effort or damage.
Understanding the range of attachments ensures that every challenge can be handled effectively, whether a lapidary beginner or a seasoned professional. Additionally, experimenting with different attachments can lead to unique techniques and designs, ultimately enriching your creative process. Thus, grasping the possibilities Dremel offers is invaluable for taking lapidary skills to the next level.
Selecting the Right Dremel Model for Lapidary
When it comes to lapidary work using Dremel tools, choosing the right model is paramount. Not all Dremel tools are created equal. Different models come with various features, capabilities, and price points, making it essential to consider your specific needs and the nature of your projects. This decision can make the difference between a captivating finished product and a frustrating experience.
Understanding the specific attributes of each model can help you optimize your crafting routine and enhance the overall quality of your work. A well-chosen Dremel not only simplifies the task but can also inspire creativity, allowing you to explore intricate designs and polished finishes with greater ease.
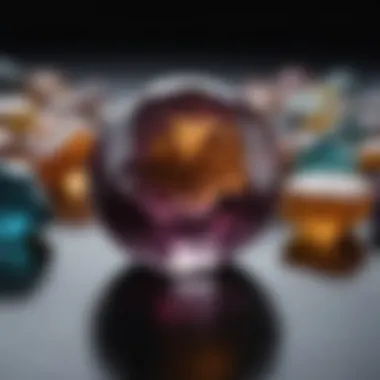
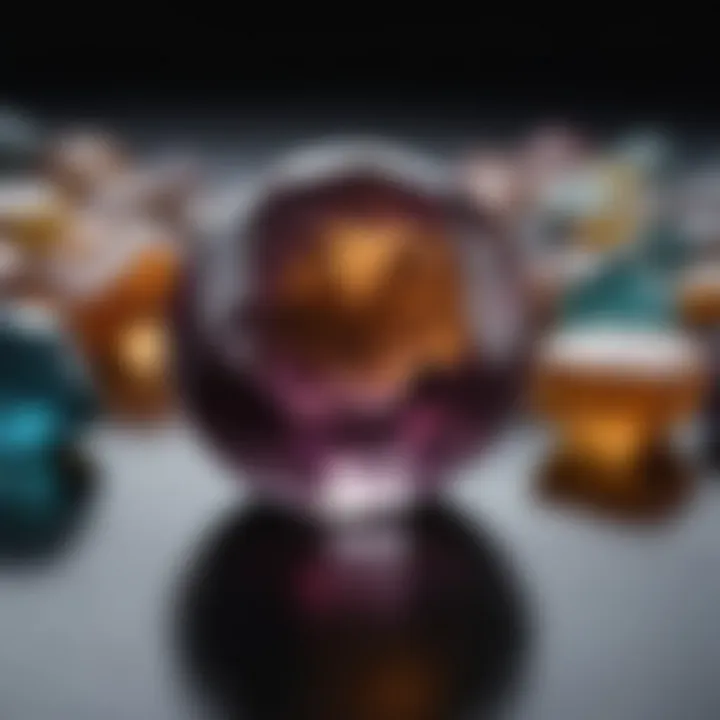
As you embark on selecting the ideal Dremel for your lapidary endeavors, think about aspects like power, speed settings, and versatility of attachments. Each of these elements fundamentally shapes your crafting experience, provides durability, and supports the quality of your results.
Key Features to Consider
To make an informed decision, you need to consider several key features when selecting a Dremel model:
- Motor Power: The horsepower of the motor plays a vital role. A more powerful motor can handle tougher materials, ensuring that you can cut and grind harder stones without straining the tool.
- Speed Variability: Look for models that offer variable speed settings. This feature allows for precision work, enabling you to adjust the speed according to the specific stone and task at hand. For instance, polishing may require lower speeds while cutting may need higher speeds.
- Attachment Compatibility: Different Dremel models may support varying types of attachments. Ensure that your model accepts grinding bits and cutting discs suited for lapidary work. This addition can widen your creative scope.
- Ergonomic Design: Comfort while working is a huge factor. A tool that feels good in your hands can mean the difference for long hours spent on projects. Look for models that offer a firm grip and lightweight design to avoid fatigue.
- Durability: Investing in a durable model will serve you better over time, especially as lapidary tools can face wear and tear from frequent use.
Some examples of models you might consider include the Dremel 4300 or the Dremel 8220. Each of these has features that cater to lapidary tasks, ensuring you can work effectively.
Comparing Popular Dremel Models
There’s a range of Dremel models available, each with its distinctive strengths. Comparing these can give you clarity:
- Dremel 4300:
- Dremel 8220:
- Motor Power: 1.8 Amps
- Speed: 5000 to 35000 RPM
- Versatility: Comes with multiple attachments and accessories, making it appropriate for an array of lapidary tasks.
- Ergonomics: Designed with a soft grip for comfort during long periods of use.
- Cordless Freedom: Runs on a rechargeable battery, allowing flexibility and portability.
- Motor Power: Offers the same robust performance as corded models but in a wireless package.
- Speed Control: Features speed settings to match different materials.
"Choosing the right Dremel model is like picking the right partner for a dance; it should complement your moves and make your performance seamless."
- Dremel 3000:
- A great entry-level machine with a good balance of power and price.
- Somewhat limited in attachments but excellent for beginners.
When selecting among these options, it’s important to remember your individual requirements and how frequently you may use the tool. Frequent users might want to invest in more advanced models, while casual hobbyists may be satisfied with simpler versions.
By weighing these features and comparisons thoughtfully, you'll set yourself up for success in your lapidary experience.
Essential Accessories for Lapidary Work
In the realm of lapidary crafting, having the right accessories can make a world of difference. Think of these accessories as the secret sauce that enhances the overall experience and effectiveness of your projects. From grinding stones to shaping rough materials, every accessory plays a crucial role in elevating your craft to higher standards.
Grinding and Polishing Bits
Grinding and polishing bits form the backbone of any serious lapidary toolkit. These items allow for precision while shaping, smoothing, and finishing stones. Different materials and grit sizes are available, offering diverse options based on the specifics of the job at hand.
- Diamond Bits: These are arguably the most popular choice. They offer a robust and durable option for grinding hard materials. Using them can significantly reduce the time it takes to achieve a polished surface, enabling hobbyists to work more efficiently.
- Ceramic Bits: Generally softer than diamond, these bits are suitable for softer stones. They tend to provide a smoother finish during the final polishing stages.
- Grit Variation: The grit of a bit denotes its roughness. Coarser bits are ideal for initial shaping, while finer grits are essential for polishing. A layered approach using various grits allows for more control over the final appearance of the stone.
When utilizing these bits, it's vital to remember that working slowly and with purpose often yields the best results. Rushing can lead to mistakes or subpar outcomes.
Cutting Discs and Their Applications
Cutting discs are another essential accessory in the lapidary workspace. They require consideration not only for the materials you’re cutting but also for the intricacies of the designs you aim to achieve.
- Types of Discs: There are various types of cutting discs, including diamond, metal-bonded, and resin-bonded. Each serves a different purpose:
- Thickness Matters: The thickness of a disc can also impact the cut. Thicker discs may offer more durability but can result in a wider cut, while thinner ones can provide cleaner lines but wear out more quickly.
- Diamond Cutting Discs are primarily used for their strength. They can slice through tougher stones with ease.
- Resin-Bonded Discs are better suited for softer materials and help in achieving smooth cuts without significant chipping.
Using cutting discs requires a steady hand and an understanding of where to apply force. It’s a balancing act between precision and pressure, making practice essential.
Choosing the right accessories is not merely about having a range. It's about understanding which tools serve specific purposes best — a skill honed over time.
Techniques for Effective Lapidary Crafting
When it comes to lapidary work, knowing the right techniques is half the battle. The intricate process of shaping and polishing stones requires not just the right tools, like your trusty Dremel, but also a set of techniques that elevate your craft from novice to expert. The significance of mastering these techniques can’t be overstated; it ensures that each piece not only shines beautifully but is also crafted efficiently and safely.
In this section, we'll explore the basics of cutting and the advanced polishing methods that can redefine your lapidary experience. Let's dive into the details.
Basic Cutting Techniques
Basic cutting techniques are essential for any lapidary enthusiast, especially when using Dremel tools. It is the groundwork upon which more advanced skills are built. To effectively cut stones, understanding the following aspects is crucial:
- Choice of Bit: Selecting the proper cutting bit, like a diamond or carbide tip, is vital. Diamond bits are excellent for harder stones, while carbide bits serve well for softer materials.
- Speed Settings: Proper speed control ensures clean cuts. Too fast, and you risk overheating and damaging the stone; too slow may lead to ineffective cuts. A general rule is to start slow and gradually increase speed as you gain confidence.
- Angle and Pressure: Maintain a steady hand while controlling the angle of your cut. Too much pressure may lead to chipping or cracking, while too little won’t deliver the desired cut.
These fundamental techniques set the stage for creating stunning shapes in your stones, providing a strong foundation upon which to build your skills. By practicing these techniques, a lapidary artisan can not only develop proficiency but also gain a deeper appreciation for the material they’re working with.
Advanced Polishing Methods
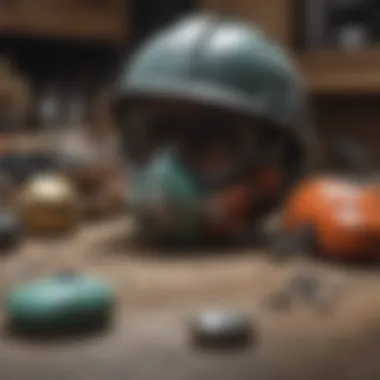
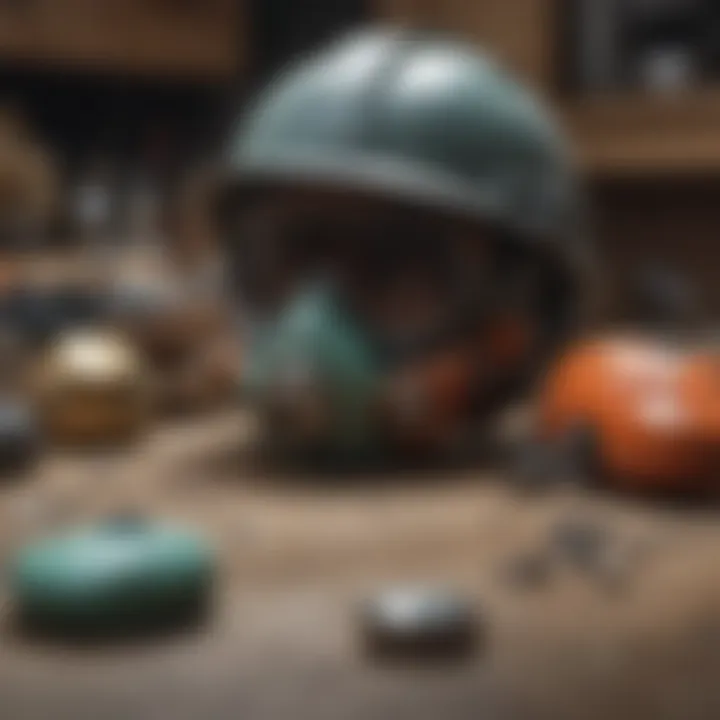
Once the cutting is done, the exciting phase of polishing begins. Advanced polishing methods can transform your rough stone into a radiant gem. Here are some pivotal techniques to consider:
- Progressive Grit Levels: Like peeling an onion, you want to start with coarser grits and gradually move to finer ones. This multi-step approach helps remove scratches from previous stages, leading to a brilliant finish.
- Dremel Polish and Compound: Use specialized polishing compounds that can be applied with appropriate bits. These compounds enhance the shine and act as a protective layer.
- Technique Adjustments: Keep the stone wet during polishing to prevent heat build-up, and always move the Dremel in circular motions to achieve an even polish.
- Begin with 80-120 grit for initial sanding.
- Progress through 220, 400, and up to 600-1200 grit for a flawless polish.
"Good polishing methods are like a secret handshake among lapidarians; they set you apart from the rest and reveal the beauty within your stones."
By honing these advanced polishing methods, lapidary creators can achieve stunning results that elevate their work. With each crafted piece, they contribute to a legacy of craftsmanship that speaks to their skill and dedication.
Incorporating both basic cutting techniques and advanced polishing methods into your practice can create an immensely rewarding lapidary experience. As you continue to refine your skills, remember that each stone has its story, and it’s up to you to bring that story to life.
Safety Precautions When Using Dremel Tools
Engaging in lapidary work with Dremel tools can yield stunning results, but with great potential comes great responsibility. It's essential to prioritize safety measures to protect yourself while manipulating these versatile instruments. Understanding the significance of these precautions not only enhances your crafting experience but also safeguards your long-term health and well-being.
Personal Protective Equipment
When it comes to lapidary work, wearing the right personal protective equipment (PPE) is a non-negotiable aspect of your safety protocol. Fitted safety glasses, for instance, should become a staple in your toolkit, as they shield your eyes from flying debris that may result during cutting or grinding. A reputable pair of goggles with side protection works wonders.
Beyond eye safety, consider wearing a dust mask or respirator. Lapidary work generates a sea of fine dust, some of it hazardous. A mask rated for fine particulates can keep you breathing easy while you focus on your craft. Don't overlook gloves; choose a pair suitable for handling tools and materials—this can prevent cuts and scrapes, which can seriously hinder working continuity.
Wearing the correct PPE can mean the difference between enjoying a rewarding project or facing serious injury. Always prioritize your safety, even if it feels cumbersome at first.
Safe Operating Practices
Understanding and implementing safe operating practices is crucial for ensuring a smooth lapidary session. Firstly, always inspect your Dremel tool before use. Check for any wear or damage, especially on the attachments, as a compromised accessory can be a recipe for disaster. If something appears off, it's worth taking the time to replace it rather than risking an accident.
Another significant practice is maintaining a clean workspace. Clutter can lead to mishaps. Keep your work area tidy and free from loose articles that might interfere with your cutting or grinding. Organize tools and materials systematically to avoid reaching across your workspace, which can cause you to lose focus.
Finally, familiarize yourself with the specific tool settings before you dive into a project. Each Dremel model offers various speeds and attachments suited for different tasks. If you’re unsure what speed to use for a particular job, consult the user manual or seek online resources that pertain specifically to lapidary applications. Properly utilizing your tools will not only ensure your safety but will also lead to better craftsmanship.
By adhering to these safety precautions, you're not merely following rules; you're fostering an environment that allows creativity and productivity to flourish without jeopardizing your well-being. Engaging in lapidary work is a rewarding hobby, so make sure to enjoy it fully and safely!
For further insights into Dremel tools and lapidary work, consider checking out Wikipedia's overview or joining conversations on Reddit.
Maintenance of Dremel Tools
Maintaining your Dremel tools is as crucial as the skill you put into your lapidary projects. Just like tending to a garden reaps the sweetest fruits, proper care ensures your Dremel lasts longer and performs at its best. Regular maintenance can save you time, money, and maybe even enhance the quality of your craftsmanship.
Regular Cleaning Techniques
Cleaning your Dremel should not feel like a chore; instead, view it as a ritual that corresponds with your creative endeavors. As you finish a project, take a moment to wipe down your tools and remove any dust or debris. Here’s how you can go about it:
- Unplug the Tool: Safety first! Always make sure the tool is unplugged or turned off before cleaning.
- Use a Soft Cloth: A soft, lint-free cloth works wonders. Gently wipe the exterior surfaces to remove dirt or grease.
- Compressed Air: For getting into nooks and crannies, a can of compressed air can be your best friend. Blast away any stubborn wood chips or stone particles that might have sneaked in.
- Inspect the Attachments: Regularly check your bits and accessories to see if they need cleaning. A small brush can also clear out dust from the numerous crevices.
- Lubricate Moving Parts: Don't forget to give attention to the rotation areas. A drop of appropriate lubricant can ensure smooth operation.
"A little maintenance goes a long way in ensuring durability and high performance in your Dremel tools."
Troubleshooting Common Issues
Even with careful maintenance, occasional hiccups might rear their ugly heads. Addressing these common problems early can prevent more severe issues and save your stone from improper treatment. Here’s how to troubleshoot when things go awry:
- Tool Not Starting: Ensure it’s plugged in, check the switch, and look for any worn-out wiring.
- Excessive Vibration: This could stem from a worn-out bit or improper attachment. Try switching the bit to see if the vibration persists.
- Overheating: If your Dremel is too hot, it may be time to take a break. Reduce the load and allow it to cool down.
- Poor Performance: If cuts are lackluster, it might indicate that your bits are dull. Replacing them can revitalize your tool’s effectiveness.
- Unusual Noises: A grinding or clicking sound can signal trouble. Look for debris caught in the mechanism, or if persistent, consult with a professional technician.
Caring for your Dremel tools doesn’t just expand their longevity; it directly impacts the quality of your lapidary work. In the grand scheme, nurturing these tools creates an environment where creativity can flourish.
Incorporating Dremel Tools into Your Lapidary Workflow
Integrating Dremel tools into your lapidary workflow represents a paradigm shift that can significantly enhance your stone crafting and polishing endeavors. The importance of this integration cannot be overstated, as it harmonizes efficiency with creativity, allowing you to explore intricate details and apply various techniques with precision.
When considering the incorporation of Dremel tools, the first element to ponder is versatility. These tools serve multiple functions - from cutting and shaping to polishing stones, they cater to a variety of tasks within lapidary work. This versatility not only streamlines the process but also diminishes the need for multiple specialized devices. Adopting a single, adaptable tool like the Dremel means you can switch from one activity to another seamlessly, reducing downtime and maximizing productivity.
Another crucial aspect is enhanced control. Dremel tools are designed with user-friendliness in mind, boasting adjustable speed settings and a range of attachments that empower creators to manipulate their materials with finesse. This control is particularly beneficial when working on delicate pieces—where the minutest adjustments can make a substantial difference.
"The key to successful lapidary work lies in the details; with Dremel tools, those details become attainable."
Furthermore, there’s the consideration of creativity. The ability to attach different bits enables you to not only grind and cut but to etch designs or engrave intricate patterns onto your stones. This opens up a realm of artistic possibilities that can elevate your work from mere craft to personalized artwork.
Planning Your Projects
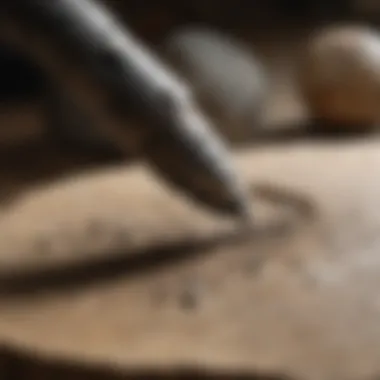
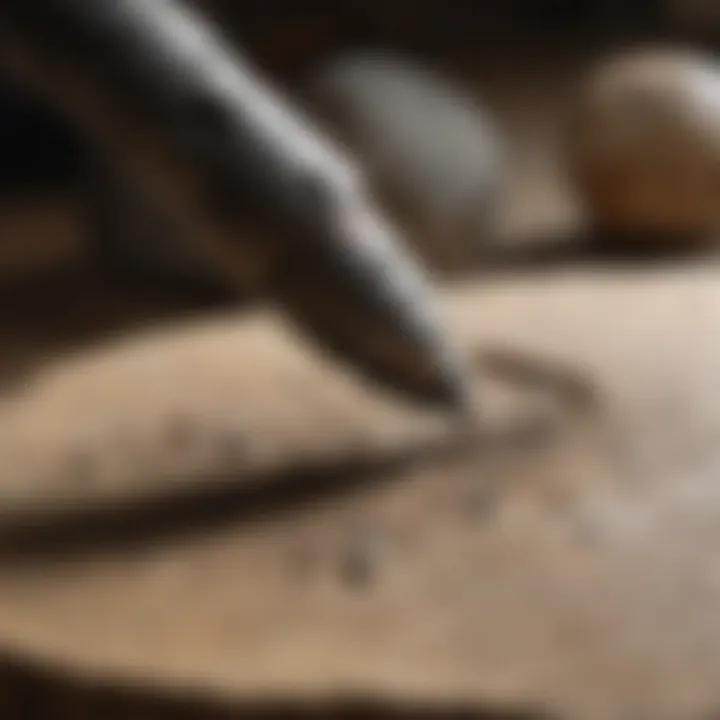
Planning your projects with Dremel tools involves a few critical steps. First off, you need to assess the gemstones or materials you plan to work with. Understanding their hardness and texture will help in choosing the right bits and speeds for your Dremel tool.
- Set Clear Goals: Before diving in, determine what you aim to create—be it smooth pendants, ornate rings, or simple cabochons. Each project requires its unique approach, so defining your objectives leads to more organized work.
- Material Selection: Each stone has its personality; softer stones like soapstone are easier to manipulate, while harder stones like jade demand a bit more respect and finesse. Match your Dremel tool settings accordingly.
- Sketching Designs: Since variety is the spice of life, sketch out your ideas. This can serve as a roadmap during the process and help visualize your end product, saving time and effort trying to figure things out on the go.
Integrating Techniques for Efficiency
To truly harness the potential of Dremel tools in your lapidary workflow, integrating various techniques becomes pivotal. This involves employing effective methods to achieve superior results while conserving energy and time.
- Batch Processing: Group similar tasks together. For example, if you have several stones to shape, handle all the grinding in one go. This approach saves not only time but also minimizes wear on your tools.
- Right Tools, Right Time: Using the appropriate attachment or accessory for each stage of your project is critical. For instance, switch to a polishing bit as you finish rough cutting to avoid backtracking or double handling.
- Time Management: Allocate time for each phase clearly. Keeping a close eye on how long you spend on each task helps improve efficiency over time and encourages you to step away from the wheel when needed to avoid errors from fatigue.
Adopting Dremel tools into your lapidary workflow is not merely a trend; it’s a step toward mastering a craft that requires patience, skill, and an acute eye for detail. By taking the time to plan and integrate various techniques, you can elevate both your capability and creativity in stonework.
Exploring Advanced Applications of Dremel in Lapidary
The use of Dremel tools in lapidary can elevate a simple craft into an intricate art form. In this section, we'll explore how these versatile tools play a crucial role in advanced applications, allowing lapidary artists to tap into their creativity while refining their techniques. Understanding these advanced applications can transform the crafting experience, making it not just productive but also deeply satisfying.
Creating Intricate Designs
When it comes to creating detailed patterns on stones, the Dremel tool stands out as a game-changer. With its precise control and a wide variety of attachments, artists can carve intricate designs that would be nearly impossible by hand. For instance, using a fine engraving bit can allow a lapidary crafters to introduce stunning details into a pendant or gemstone, turning a simple piece into a captivating focal point.
Implementing techniques like undercutting can add depth and dimension to your pieces, enhancing their visual appeal. The ability to manipulate the speed of your Dremel tool means you can work with different techniques, from fast cuts for rough shaping to slower, more deliberate movements for fine detailing.
Benefits of Using Dremel for Intricate Designs:
- Precision: Offers unmatched accuracy for detailed work.
- Versatility: Suitable for both small and large projects.
- Customizability: The swapsies of bits make it easy to evolve your design as you go.
"Talent is important, but the right tools can amplify creativity in lapidary work."
Furthermore, the Dremel's portability allows for convenient adjustments on-the-go. Whether you're at home or at a local rock club workshop, the ease of traveling with a Dremel makes it a preferred choice among many hobbyists and professionals alike.
Combining Materials and Techniques
One of the wonders of lapidary is the ability to play with various materials. Dremel tools afford creators the flexibility to combine different elements, such as gemstones and metals. For example, you could create a mixed-media piece that incorporates both a polished agate slice and copper wire wrapping. By using the cutting discs and grinding attachments offered by your Dremel, transforming raw materials into cohesive artistic pieces becomes a thrilling journey.
Incorporating different techniques—like mixing the use of the polishing cloths and diamond-tipped bits—can further enhance the final output. Each material responds differently, and understanding how to work with each will ensure better results and more interesting designs.
When plunging into material combinations, it's wide to consider the hardness and texture of each element. This consideration impacts everything from the speed you use to the type of bits suitable for cutting or engraving.
Considerations for Combining Materials:
- Compatibility: Not every material works well together, so it's important to proceed with care.
- Weight Distribution: Balance out heavier stones with lighter materials to avoid an awkward end product.
- Finishing Techniques: Each material requires a different finishing touch, so plan accordingly.
By mastering the blend of techniques and materials with Dremel tools, lapidary artists can carve out their niche in the vast world of craft. This breadth not only enriches your artistic journey but also opens doors for unique creations that resonate with your personal touch.
Community Resources for Lapidary Enthusiasts
In the world of lapidary, being part of a community can make all the difference. While the tools and techniques you employ on your lapidary journey are essential, so too are the people with whom you share that journey. Community resources not only provide support but also open avenues for learning, collaboration, and experimentation. From newbies seeking guidance to seasoned pros exchanging insights, the right forums, groups, workshops, and clubs can enrich your lapidary experience.
Online Forums and Groups
Online forums and groups serve as virtual meeting places where lapidary enthusiasts from around the globe converge. These platforms offer various benefits:
- Knowledge Exchange: Members post queries about techniques and tools, leading to discussions that can help you solve problems you may encounter in your own projects.
- Resource Sharing: You might come across tutorials, videos, or even articles that others have found useful. It’s like having a treasure trove of information at your fingertips.
- Networking: By engaging in these communities, you can form connections with fellow enthusiasts who share your passion.
For instance, Reddit hosts multiple communities such as r/lapidary where individuals not only seek advice but also share their latest creations, paving the way for constructive feedback. Similarly, groups on Facebook attract diverse participants, each bringing their perspective and experience
The End: Mastering the Art of Lapidary with Dremel Tools
Mastering the art of lapidary work with Dremel tools stands as a pivotal conclusion to this extensive exploration. It encapsulates the journey of honing skills, understanding techniques, and the nuances of tool operation and maintenance. The Dremel isn't just a tool; it's a gateway to transforming raw stones into polished gems, each piece telling its own story.
As we dissected throughout the article, the versatility of the Dremel tool allows for a wide range of applications in lapidary work. From precise cutting to fine polishing, mastering its use can significantly enhance both the quality of craftsmanship and the enjoyment of the craft itself. Take note that choosing the right attachments, and utilizing the appropriate techniques, can elevate your work to new heights. The ability to create intricate designs and seamlessly combine different materials further exemplifies the possibilities at your fingertips.
In this journey, safety has also been emphasized as a non-negotiable element. Proper equipment and practices not only ensure the longevity of your tools and health but also ultimately contribute to a more satisfying lapidary experience.
The merging of these elements underscores the importance of dedication in mastering lapidary techniques with Dremel tools. Every gem you craft, every polished finish you achieve, is a testament to your commitment, creativity, and the skills harnessed along the way.
"The only limit to your impact is your imagination and commitment."
Key Takeaways
- Versatility: Dremel tools offer functionality for both simple and complex lapidary tasks, leading to diverse and artistic expressions.
- Craftsmanship: Mastering the use of accessories and techniques influences the final product's aesthetic and quality.
- Safety and Maintenance: Prioritizing safety and proper care for tools directly impacts the effectiveness of your workmanship and your personal well-being.
- Community and Resources: Engaging with fellow lapidary enthusiasts provides insights, support, and inspiration to unlock your full potential.
Encouragement to Explore Further
For those who find an eagerness to delve deeper into the world of lapidary art, a wealth of resources awaits you. From online platforms, such as forums on Reddit, to local workshops listed on sites like Facebook, there's no shortage of avenues for learning and connecting with others who share your enthusiasm. By immersing yourself in these communities, you can acquire tips, troubleshoot common problems, and discover innovative techniques that take your craft to the next level.
Additionally, visiting informative pages like Wikipedia or Britannica can provide historical context and a breadth of information about lapidary practices worldwide. Remember, the more you invest in learning about this craft, the more beautiful creations you can make.