Crafting a Casting Mold: A Complete Guide
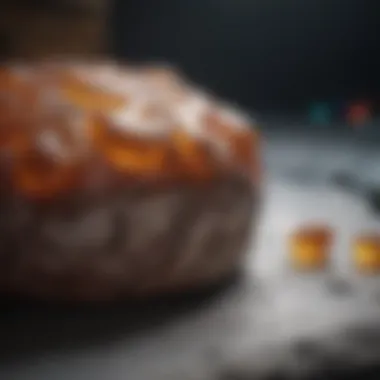

Intro
Creating casting molds can be both an art and a science. For those who delve into the world of collectibles, especially rock and fossil enthusiasts, understanding this craft is paramount. Crafting a casting mold goes beyond merely duplicating an object; it involves painstaking attention to detail and a comprehensive knowledge of materials and techniques that can greatly influence the final product.
In this guide, we will explore the multifaceted process of designing and producing casting molds. We will discuss various materials, their properties, and the techniques for effective mold-making, ensuring that every step is clear and accessible. From beginners wanting to learn the ropes to experienced hobbyists seeking to refine their skills, there are valuable insights ahead.
Overview of the Topic
Definition of Key Terms
Before diving deeper into the craft itself, it’s crucial to establish some foundational terminology.
- Casting Mold: A hollow form that is used to shape liquid material, allowing it to solidify into a particular design or replica.
- Resin: A synthetic substance often used due to its versatility and durability in mold-making.
- Release Agent: A substance used to prevent the mold material from sticking to the object being replicated.
Historical Significance
Casting molds have a rich history, dating back to ancient civilizations. The Egyptians, for instance, used molds for creating intricate jewelry and tools. Similarly, the art of replicating objects using molds has been preserved through centuries, evolving with advancements in material science and technology. Today, collectors are leveraging these age-old techniques to recreate everything from rare fossils to unique rock formations.
"The beauty of casting molds lies not just in the creation but in the preservation of history itself."
Types of Collectibles
Classification of Different Collectibles
Within the realm of collectibles, mold-making can serve various purposes. Some of the notable categories include:
- Fossils: Natural imprints that tell a story of ancient life. Replicating these allows enthusiasts to own a piece of history.
- Rocks and Minerals: Many collectors focus on rare specimens, and having a mold can help in creating exact replicas for study or display.
- Antiques and Vintage Items: Molds can also be used for reproducing classic items that are not easily found in the market.
Notable Categories
The world of collectibles is vast, but here are some significant categories worth noting:
- Minerals: Unique specimens that derive their value from their rarity and condition.
- Fossils: Molds can capture intricate details of ancient creatures and plants.
- Artistic Replicas: Many collectors appreciate the artistry involved in reproducing well-known works using molds.
The significance of accurately crafting molds from these collectibles cannot be overstated; it allows for appreciation and study without damaging the original pieces. As we delve deeper into this guide, we will break down materials and techniques essential for startup in molding, aiding both hobbyists and dedicated collectors in scaling their craft.
Prelude to Casting Molds
Casting molds play a crucial role in the broader world of material crafting and artistry, particularly within the realms of collectibles and fossil replication. Understanding these molds fuels creativity, expanding the horizons for hobbyists and professionals alike. When considering what it takes to create a casting mold, one must think about the methods, materials, and outcomes that contribute to successful replication of original items.
Definition of Casting Molds
Simply put, casting molds are templates used to shape a material into a desired form. When you’re pouring a liquid substance into these molds—be it silicone, resin, or plaster—the material takes on the exact contours of the mold. This technical definition, however, hardly captures the excitement and artistry involved in the process. Think of a mold as an artistic collaborator, working alongside you to reproduce the beauty of unique natural shapes or crafted objects. Whether replicating an intricate vintage figurine or a rugged fossil, these molds allow creators to preserve and share their passions with others.
Importance of Casting in Collectibles
The significance of casting in creating collectibles cannot be overstated. For collectors, having the ability to replicate rare items can mean the difference between possessing fleeting dreams and realizing tangible creations. Notably, replicating collectible items helps keep the hobby alive, offering new generations a chance to experience what once was. The process also democratizes access to art, allowing enthusiasts to craft bespoke pieces rather than purchase expensive originals.
"Replicating items not only satisfies the collector's urge but also allows for exploration into the creativity of the collector."
Moreover, launching into casting can open doors to personal expression, letting you put your unique spin on traditional designs. From choosing the materials that suit your style to deciding how closely to stay to the original, each step offers space for innovation. In summary, the art of casting molds isn’t just a repetitive task; it’s a gateway to a vibrant community of creativity.
Types of Casting Molds
Understanding the different types of casting molds is fundamental for anyone looking to get into mold making. Each type offers unique characteristics that cater to specific projects, thus enhancing the casting experience. Choosing the right mold plays a critical role not just in replicating an object but also in the overall durability and quality of the final product. This section illuminates the nuances of rigid molds, flexible molds, and the intriguing process of reproducing natural shapes.
Rigid Molds
Rigid molds are typically crafted from sturdy materials like plaster, metals or certain kinds of polymers. Their strength provides an advantage when casting materials that require a stable environment to cure properly. For instance, when creating a mold for a resin cast, a rigid mold can withstand the weight and pressure without warping or bending.
One of the key benefits of using rigid molds is the precision they offer. They allow for intricate designs to be captured without distortion. It's important, however, to ensure that the original item to be replicated is strong enough to withstand the pouring process without being damaged. The downside? You can face challenges when it comes to demolding, especially for complex shapes. Here are some points to consider:
- Durability: Rigid molds can last through numerous uses if maintained properly.
- Detailing: Ideal for intricate items where fine detail is crucial.
- Weight: They can be heavy and cumbersome to handle.
Flexible Molds
In contrast to the rigidity of their counterparts, flexible molds offer an entirely different set of advantages. Commonly made from materials like silicone, these molds can bend and stretch, allowing for smooth extraction of cast items regardless of the shape. This flexibility is particularly appealing when creating complex or delicate designs that could easily break in a more rigid mold.
A notable advantage of flexible molds is their ability to capture intricate details with remarkable fidelity. However, the trade-off lies in their lifespan, as they may degrade faster than rigid options. The following benefits make flexible molds a popular choice for hobbyists and professionals alike:
- Ease of Use: You can remove casts easily without damaging them.
- Versatility: Perfect for casting materials like resin, plaster, and even wax.
- Durability: Generally good but can wear out with frequent use.
Reproducing Natural Shapes
The ability to replicate natural shapes opens a world of possibilities, particularly for rock and fossil collectors. This technique enables artisans to create highly realistic items that mimic their organic counterparts. Typically involving special techniques and tools, reproducing natural shapes entails capturing the intricate details found in nature, such as textures and contours.
A significant factor that enhances this process is the use of both rigid and flexible molds. A combination of these types can often yield the best results. For instance, a rigid outer mold can encase a flexible inner mold. This allows for easier demolding while maintaining the aspect of detail.
Here are some elements to think about when reproducing natural shapes:
- Material Selection: Choosing materials that will properly convey the natural textures of the object.
- Focus on Detail: Using a flexible mold can help capture the minutiae of an organic feature, such as the lines on a leaf or the ridges on a fossil.
- Experimentation: Don't be afraid to try different combinations of materials and techniques.
It's vital to recognize that selecting the right type of mold can significantly impact the quality of your casting project. Understanding these differences helps ensure you achieve your desired results.
By having a solid grip on the types of casting molds available, hobbyists can make informed decisions that align with their project requirements. Ultimately, the choice between rigid and flexible molds, along with the ability to reproduce natural shapes, establishes a solid foundation for successful mold-making.
Materials for Making Casting Molds
Casting molds are the backbone of any great project for collectors and artisans alike. Choosing the right material not only determines the quality of the finished mold but also impacts the entire workflow from start to finish. Each type of material brings its unique set of characteristics, benefits, and challenges. Therefore, understanding these materials is essential for making informed and effective decisions.
Silicone Rubber
Silicone rubber has gained recognition as one of the most versatile materials for making molds. Its flexibility and durability allow it to capture intricate details from original items, which is particularly beneficial for those seeking to replicate collectibles or fossils. What makes silicone rubber stand out? It is resistant to tearing, can withstand high temperatures, and boasts excellent resilience. Additionally, it is a non-toxic option, making it safer to work with.
While it may be on the pricier side compared to other materials, the long-lasting nature and ease of demolding justify the investment. A word to the wise: pay attention to the specific type of silicone you’re using. For instance, platinum-cured silicone offers superior curing properties but may require special handling.
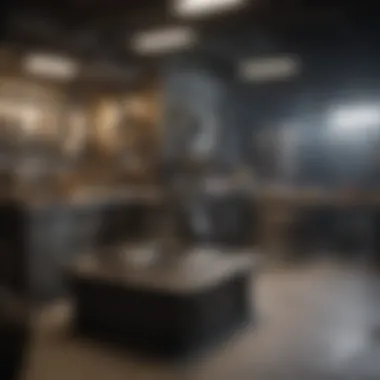

Plaster of Paris
Plaster of Paris is a classic in the mold-making realm, known for its inexpensive and easy-to-use nature. It provides a smooth finish and is particularly effective for making rigid molds. However, it does have limitations. It is not suitable for high-detail work and is susceptible to water damage, meaning its durability is often questioned.
What’s notable about Plaster of Paris is its speed of setting. It starts firming up quickly, allowing mold makers to work efficiently. Yet, it requires some know-how to avoid issues such as cracking. Besides that, a solid release agent is essential to prevent the model from sticking.
Resin
Resin can be an outstanding option when aiming for exceptional longevity. This material is often favored for its rigidity and ability to capture fine details flawlessly. When cured properly, resin molds can endure stress and wear, making them ideal for repeated use in casting.
However, working with resin does carry its risks. The fumes can be potent, necessitating adequate ventilation and protective equipment. Moreover, the curing time can vary significantly depending on the type of resin you’re using.
There are numerous varieties of resin available, each with its own setting time and viscosity. Epoxy and polyurethane are two common choices. Epoxy has a longer curing time but offers a clearer finish, while polyurethane cures more quickly but can be a bit cloudy depending on the mixture.
Metals for Molds
Metal molds are often overlooked but can offer robust solutions for specific casting projects. They excel in producing precise and durable molds that can handle high-temperature applications. For collectors working with materials that require a rapid cooling time, metals like aluminum or steel can be excellent choices. They not only enable efficient casting but also provide a sturdy base for repeated use.
However, metal molds do have their own intricacies. The initial cost can be sky-high, and the process of fabricating a metal mold can be much more complex than its counterparts. Metal molds also require a good understanding of release agents to ensure easy removal of cast material.
Additionally, working with metals may necessitate welding or machining skills, which could deter novice mold makers. Regardless, for those ready to take the leap into more advanced techniques, the results can be well worth the effort.
"The right material can make or break the mold."
In summary, when contemplating materials for casting molds, it’s vital to evaluate your project’s specific needs. From the detail level you desire to the durability requirements, each material presents its pros and cons. By weighing these factors adequately, mold makers can make choices that align with their artistic vision and practical needs.
Tools Required for Mold Making
When it comes to crafting a casting mold, having the right tools can make or break your project. Whether you're a rock or fossil collector aiming to replicate your prized specimens or simply trying your hand at a new hobby, understanding the tools is essential. This segment will explore the fundamental tools needed, emphasizing their importance, benefits, and considerations.
Mold Boxes
Mold boxes serve as the foundational structure for your mold-making process. Think of them like the frame of a house; without it, everything would collapse. Typically constructed from materials such as wood, plastic, or sturdy cardboard, these boxes hold the original model in position while the mold material cures. Their benefits include:
- Stability: A mold box keeps your shape intact and prevents leakage during the pour.
- Size Control: You can customize the dimensions of the box to accommodate various project sizes.
- Reusability: With careful construction, you can use the same box multiple times, saving both time and resources.
However, remember that not all mold boxes are created equal. If you’re working with highly detailed models, it's wise to invest in something robust that won’t bend or break under pressure. An important consideration is sealing; ensure it fits tightly.
"A good mold box is as important as the mold itself; it shapes the journey before the product even starts setting."
Mixing Tools
Once the mold box is ready, the next step involves mixing your mold materials. Having precise mixing tools is vital for achieving the right consistency. Here are the main tools you’ll need:
- Measuring Cups and Spoons: Accuracy here can't be overstated. Doses matter, especially with chemical resins or silicones.
- Mixing Sticks: Simple yet effective, these are usually made from wood or plastic. They allow for thorough mixing, preventing lumps that could jeopardize mold integrity.
- Bubbles Popper or Spatula: Air bubbles can ruin a mold. A bubble popper or a spatula can help push air out during mixing, ensuring a smoother finish.
It’s critical to follow specific instructions regarding mixing times and ratios. In some cases, even a slight variation can lead to inadequate curing or a poor-quality mold.
Release Agents
When it comes time to demold your creation, this is where release agents come into play. These substances help prevent the mold material from sticking to the original model or the mold itself, ensuring an easy release and prolonging the life of your molds. Common release agents include:
- Petroleum Jelly: A household staple that does wonders for basic silicone molds. Just a thin film applied can do the trick.
- Commercial Release Sprays: Handy products available at craft stores, these sprays provide a no-fuss application. Check they're compatible with your chosen materials.
- Waxes: High-quality wax applied to the original item forms a barrier, ensuring no unwanted sticking.
It's worth repeating that using a release agent isn’t just for convenience; it can significantly impact the longevity of your molds while minimizing damage during the demolding process.
By equipping yourself with the right tools—mold boxes, mixing tools, and release agents—you set yourself up for success in mold-making. Each element plays a critical role in ensuring that your casting endeavors are smooth sailing.
Preparing for Mold Making
Preparing for mold making is a crucial step in the overall casting process. It’s not just about gathering materials and tools; rather, it’s about carefully considering each aspect that contributes to a successful mold. A well-prepared approach can save time, materials, and frustrations down the line.
Selecting the Original Item
The first step in preparing for mold making is selecting the original item. This choice is pivotal because the quality and details of this item will directly influence the final product. Look for something well-defined and unique to capture the essence in your mold.
When selecting the original, consider the following:
- Size and shape: Ensure it fits comfortably within your mold box without excessive overhang.
- Material properties: The item's surface must be conducive to mold making—no cracks, absent pieces, or overly porous textures.
- Significance: If you're creating a mold for collectibles, choose items that have sentimental or economic value, as this encourages careful handling.
When you find the right piece, you’ll know it instantly. It should resonate with the vision you have for the final casting.
Cleaning and Prepping the Original
Cleaning the original item is another fundamental aspect of preparing for mold making. Any dust, grease, or residue will affect both the process and the quality of the mold. A dirty item can lead to air bubbles or an incomplete cast, which no one wants after spending significant time and resources.
Here are some important steps in cleaning:
- Dusting: Use a soft brush or cloth to remove dirt.
- Washing: If the item allows, clean it with soap and water. Ensure it’s fully dried afterwards.
- Inspecting: Check for any flaws or damages.
By taking these steps, you help ensure a smooth transfer of details into your mold. Remember, a clean start leads to a clean finish.
Designing the Mold Structure
After you’ve selected and cleaned the original item, it’s time to design the mold structure. This stage is where your creativity and technical skills intersect. The mold structure should accommodate the original item and provide optimal detail retention.
Considerations for designing your mold structure include:
- Type of Mold: Will it be a single part or multi-part mold? Single part molds are simpler but may limit complexity in the design. Multiple parts can capture intricate details.
- Mold Box Dimensions: Ensure the mold box is spacious enough to allow the material to flow freely around the original item, preventing areas from being left uncovered.
- Draft Angles: Sometimes, a slight angle can help with the removal of the mold after curing without risking damage to both the mold and the original.
Design is where the magic begins, transforming your artistic vision into a tangible object. Plan thoughtfully, and the outcome can be truly rewarding.
The Mold Making Process
Understanding the mold making process is a pivotal part of creating effective casting molds. This section unfolds the intricate steps involved, which form the backbone of successful casting. Without a solid grasp of this process, even the best materials can go to waste. Effectively preparing a mold ensures a clean and accurate reproduction of the original item, essential for anyone serious about collectibles or fossil replication.
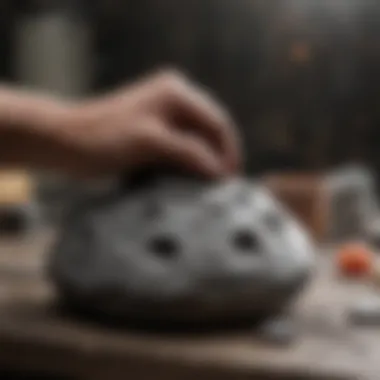

Creating a Mold Box
The first step in building a mold box is selecting the right dimensions. A mold box, also known as a mold container, is the foundation on which the mold is built. Ideally, it should fit your original item snugly but allow for enough clearance on all sides. Consider using materials like acrylic sheets or wood; these options provide rigidity and prevent leakage.
- Measure accurately: Take precise measurements of the original item and add at least a half-inch on all sides. This extra space accommodates the thickness of the casting material.
- Assemble with integrity: When constructing your mold box, ensure that joints are tightly secured. Any gaps could lead to material seeping, resulting in an uneven mold, which can cost both time and material.
Mixing the Mold Material
Once the mold box is ready, attention turns to mixing the mold material. Proper mixing is crucial—it is the heart of the mold-making process. Common choices here are silicone rubber or plaster, each offering unique benefits. Silicone is both flexible and durable, while plaster might suit simpler, less complex designs.
Key considerations:
- Follow instructions thoroughly: Each material comes with its mixing ratios and guidelines. Deviating from these can alter softening or curing times.
- Ensure a thorough mix: Use a spatula or mixing stick to combine the components well. A uniform mix will prevent toughening in one area while remaining soft in another, which could jeopardize the final product.
Pouring the Mold Material
After mixing, it’s time to pour. The pouring technique is very important. The goal here is to minimize air bubbles and achieve a perfect silhouette of the original item.
- Pour slowly: Avoid hasty actions; pour the material at a slow and steady pace. Pouring from the corner allows for bubbles to escape more easily.
- Vibration helps: Should you wish, gently tapping the mold box helps shake free any air pockets that may have formed during the mixing.
Pro tip: pouring from a height helps to break surface tension, further reducing the chances for bubbles.
Curing and Setting Time
This period cannot be rushed; curing is when your mold material transforms from a liquid state into a solid form. It’s critical to follow the manufacturer’s suggested curing times, as this will ensure the mold reaches its optimal strength.
- Factors influencing cure time: Humidity, temperature, and the type of material dictate how quickly a mold cures. Warmer, dryer conditions typically result in faster curing.
- Avoid displacement: While the material cures, resist the urge to touch or move the mold. Any disturbance could lead to imperfections in the final product.
Remember, the success of your casting endeavor hinges significantly on the effectiveness of every step in the mold making process. Take time to execute each stage with precision and care.
This intricate process from creating mold boxes to pouring and curing reflects the level of commitment required for fostered quality in reproduction, whether it be for collectibles or lifelike fossil replicas.
Finishing the Mold
Finishing the mold is a critical phase in the mold-making process. It is often said that the devil is in the details, and this holds true for mold crafting. A well-finished mold not only enhances the quality of the cast but also extends the mold's lifespan. It involves several key steps, including removing the original model, trimming and cleaning the mold, and ultimately testing it with casting material. Each step is essential to ensure that the mold serves its purpose effectively, creating high-quality replicas with precision.
Removing the Original Model
The first task in this finishing stage is the delicate removal of the original model. This process requires caution and patience. Depending on the material of both the mold and the model, one must proceed carefully. If the mold is made from a flexible material like silicone, it can often be peeled away from the original without much fuss.
However, if one has used a rigid mold like plaster, the situation is a bit trickier. Breaking the mold away requires a bit more effort and can risk damaging your original model. Always ensure that you have sufficiently cured your mold material before attempting removal.
"Patience is a virtue" – this saying rings true; rushing can lead to mishaps that could ruin your entire project.
Trimming and Cleaning the Mold
Once the original model is out, it's time to tidy up the mold. Trimming away any excess material is crucial. Look for any jagged edges or unwanted material that could affect the final casting. Scissors or hobby knives often do the trick. Take care, though! Precision is key. You want your finished mold to be as smooth as possible, or else it might create imperfections in the final cast.
Cleaning the mold might sometimes involve mild soap and water, depending on what material you have used. This step prepares the mold for future use. If any residue from the original model is left behind, it can compromise the integrity of the cast material.
- Inspect for any debris that might have settled in.
- Use soft brushes or cloths to avoid scratching the mold surface.
Testing the Mold with Casting Material
Testing the mold is like trying on shoes before you buy them. You want to ensure that everything fits just right. Pour a small amount of your casting material into the mold. This allows you to check for any issues that may arise before doing a full casting. During the test, observe how the material fills the mold. Are there any air pockets? Is the mold leaking? These insights are invaluable and might save a lot of headaches later on.
- Use a small batch of your casting material for testing.
- Carefully observe and take notes on the filling process, including drying times.
In short, finishing the mold is not merely an afterthought. It's a comprehensive process that, although may seem tedious, is pivotal for achieving high-caliber results in your mold-making endeavors. By paying attention to these details, you'll yield superior results that can truly impress fellow collectors or serve as a foundation for further creativity in your casting projects.
Common Challenges in Mold Making
Creating a casting mold, while a rewarding process, comes with its own set of challenges that can significantly impact the quality and effectiveness of the final product. Understanding these challenges is crucial for anyone looking to master the craft, particularly collectors and hobbyists. The common issues one might face during this intricate process include air bubbles, incomplete molds, and the durability of the mold itself. By addressing these challenges head-on, one can enhance both the quality of their casts and their overall experience in mold making.
Air Bubbles and Their Prevention
Air bubbles are one of the sneakiest adversaries in mold making. They can pop up seemingly out of nowhere, creating unwanted imperfections in the final piece. Air bubbles usually occur during the pouring phase, often due to the mold material being too viscous or not being poured slowly enough.
To tackle this issue, consider the following strategies:
- Vibration or Tapping: Once you've poured your material, lightly tap the sides of the mold box or use a vibrating table to encourage air bubbles to rise and escape.
- Vacuum Chamber: Employing a vacuum chamber can help remove air trapped in the mix before it hits the mold. While this might seem like overkill for smaller projects, it proves beneficial for advanced collectors.
- Slow Pouring: Always pour slowly and steadily. Let gravity do its work; pouring from a height can introduce air into your mix.
Utilizing these techniques can minimize air bubbles, leading to cleaner, more precise casts.
Dealing with Incomplete Molds
Encountering incomplete molds is another pesky issue that can leave mold makers feeling frustrated. This problem often arises when the original object has intricate details or recesses that the mold material fails to capture completely.
Here are some tips to avoid such setbacks:
- Thoroughly Design the Mold Structure: Before you even begin the process, take time to design your mold box with all necessary details. Ensure it can accommodate the object fully, leaving no area uncovered.
- Use the Right Thickness: When mixing your materials, make sure to apply enough thickness to capture all details. A thin layer might dry before it finds time to seep into every nook and cranny of the original item.
- Check for Entrapped Air: Before the mold sets, inspect it carefully to ensure there are no visible air pockets.
Taking these precautions can save time and materials, preventing the disappointment of a partially formed mold.
Maintaining Mold Durability
Durability in molds is vital for producing high-quality casts repeatedly. A brittle mold can crack or break, rendering it useless after just a few uses. Mold durability hinges on materials selection, proper care, and proper handling during the casting process.
Here's how to enhance your mold's longevity:
- Use Quality Materials: Always invest in high-quality materials, whether silicone, plaster, or resin. The longevity of your mold often depends on the materials chosen for the job.
- Store Properly: Mold storage is often overlooked. Keep them in a cool, dry place away from direct sunlight or extreme temperatures. Proper storage can prevent deterioration.
- Use Release Agents Wisely: Apply a proper release agent before pouring your casting material. This not only eases the extraction of the final piece but also reduces wear on the mold itself.
By focusing on these aspects, you can keep your molds in great shape, allowing you to enjoy a seamless mold-making experience and achieve consistent results with every project.
Advanced Techniques in Mold Making
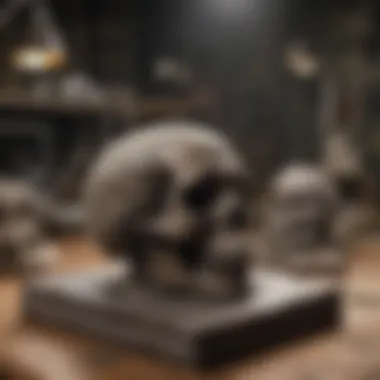

When diving deeper into the craft of mold making, understanding the advanced techniques is like opening a treasure chest of possibilities. These techniques can elevate your creations, allowing for greater detail and complexity in the final cast. Getting into the nitty-gritty of advanced mold techniques not only enhances your artistic expression but also caters to specific needs—be it for collectibles or lifecasting. They can be the difference between a standard mold and a detailed reproduction that shines.
Multi-Part Molds
Creating multi-part molds is a game-changer when dealing with intricate or larger original items. Imagine having a beautifully detailed sculpture. A one-piece mold may not capture all the delicate features without risking damage to the original. Instead, a multi-part mold allows for the careful reproduction of every little bump and curve.
- Precision: With multiple sections, each mold part can fit together perfectly, ensuring that details are not missed. Each seam must be designed to align snugly, which results in a cleaner finish.
- Complex Shapes: Items with undercuts or complicated shapes, like a frog figurine or an ornate vase, require this method. It prevents getting stuck during removal, which is crucial for preserving the integrity of both mold and original item.
- Customization: You can remove or add parts of the mold to suit new casting scenarios. If you decide to create variations or custom pieces, multi-part molds flexibly accommodate changes.
Crafting a multi-part mold does involve a bit of planning. It’s advisable to sketch out the design beforehand and consider how each part will interlock. Tools like clay can help to prototype the gates, which are vital for pouring the casting material.
Lifecasting for Organic Forms
When it comes to capturing the essence of the human body or the natural world, lifecasting presents a fascinating process. This advanced technique involves taking a mold from a living subject.
- Realism: Lifecasting creates an accurate representation, ideal for artists or collectors wanting to immortalize a loved one’s hand, or even a pet's paw print. The lifelike detail is staggering.
- Process: First, a thick layer of silicone or alginate is applied to the skin. This captures every minute detail, even texture!; after curing, the mold is carefully removed. It’s essential to work quickly, especially with alginate, as it has a rapid curing time.
- Creative Opportunities: Artists can then fill these molds with various materials like plaster, resin, or silicone for stunning results. Lifecasting can also be used for educational purposes, like anatomical models.
While lifecasting is an exciting field, it does come with unique ethical and safety challenges. Always ensure consent from subjects and be cautious of potential allergies to mold materials.
Thermal Molds for Resin Casting
In the realm of resin casting, thermal molds stand out. This technique optimizes heat manipulation to achieve effective results, especially for resin that requires specific temperature settings to cure properly.
- Heat Retention: Thermal molds, often made from specific metals or heated materials, keep the resin warm during the curing process. This can help achieve a clear and bubble-free final result.
- Increased Longevity: The durable nature of these molds means they can withstand multiple uses. Unlike silicone molds that may degrade over time, thermal molds maintain their form and functionality through various casting sessions.
- Versatility: Designs can vary from industrial uses to artistic endeavors, proving their adaptability. Whether you’re creating custom jewelry or replica fossil pieces, these molds offer a consistent experience.
For optimal results, temperature gauges are often employed to monitor the resin as it cures. This is where a little technical knowledge comes into play, but the outcomes are well worth any extra effort.
"Understanding these advanced techniques extends your capacity—and creativity—far beyond simple mold making, allowing your projects to reach unforeseen heights."
By exploring these advanced techniques, mold makers can push creative boundaries, ultimately achieving refined results. Matching tools and materials with methods could be the key to turning a basic project into a signature piece. Embracing these complexities enhances not only personal skills but fosters unique developments in the art of mold making.
Safety Considerations in Mold Making
Creating casting molds can be a rewarding process, but safety is a critical part of the journey. Engaging in mold making poses certain risks, particularly when dealing with various materials and chemicals. Understanding these safety considerations isn’t just about avoiding mishaps; it’s about fostering a mindful approach to mold making that protects both the individual and their working environment. In this section, we will delve into the essential aspects of safety, emphasizing the importance of protective wear, adequate ventilation, and safe handling of materials.
Protective Gear and Equipment
When embarking on the mold-making journey, being decked out in the right protective gear is not just smart but mandatory. The first line of defense against any potential hazards includes:
- Gloves: Opt for nitrile or neoprene gloves. These materials offer protection against most chemicals and can handle the rigors of molding materials.
- Safety Goggles: Eye protection is essential, particularly when pouring or mixing materials. Splashes can occur, and it’s vital to shield your eyes from any unexpected chemical contact.
- Dust Masks or Respirators: Certain materials can release dust or fumes that are harmful when inhaled. Depending on the substance, a basic dust mask or a proper respirator might be needed.
- Aprons: Wearing a durable apron can protect your skin and clothing from both chemicals and debris.
The idea is clear: a little preparation goes a long way in ensuring a safe working environment. Ignoring basic protective measures can lead to unnecessary accidents, which can certainly spoil the fun of mold-making.
Ventilation Needs
When mold making gets underway, good ventilation is paramount. Many casting materials, particularly resins and certain types of adhesives, emit fumes that can be hazardous when inhaled in larger quantities. Here are a few tips for maintaining airflow in your workspace:
- Windows Open: If you can, keep your workspace ventilated by opening windows. This helps in circulating air, preventing fume build-up.
- Fans: Setting up box fans or exhaust fans can foster a more significant flow of air, especially if you don’t have windows available.
- Work Outside: If the weather permits, working outdoors can be a great solution. Not only does it provide natural ventilation but it also allows you space to spread out your materials.
A well-ventilated workspace not only protects your health but also enhances your overall mold-making experience. Fumes can dampen even the best enthusiasm!
Handling Chemicals Safely
Handling chemicals isn't just about wearing gloves and goggles. It involves a comprehensive understanding of what each chemical is and how to deal with it properly. Here are fundamental practices to keep in mind when working with casting materials such as silicone, resins, or adhesives:
- Read Material Safety Data Sheets (MSDS): Always familiarize yourself with the safety data for each material. These sheets provide crucial information about safe usage, storage, and emergency measures.
- Labeling: Keep all chemicals clearly labeled. This prevents accidental misuse and enables you to spot any hazardous substances quickly.
- Proper Storage: Store chemicals in a cool, dry place away from direct sunlight. Some chemicals can degrade or become hazardous if exposed to unsuitable conditions.
- Spill Kits: Consider having spill kits readily accessible. Acting swiftly in case of a chemical spill can make a significant difference in terms of preventing a harmful situation.
In summary, safety in mold making is a multi-faceted endeavor that encompasses wearing the appropriate gear, ensuring proper ventilation, and handling chemicals with utmost care. Getting your ducks in a row before diving in can save you from a world of hurt later on.
Applications of Casting Molds
The ability to create casting molds plays a vital role in various creative and collectible industries. The versatility of casting molds opens doors to unlimited possibilities, allowing individuals to reproduce specific shapes, designs, and even textures that would be otherwise difficult or impossible to replicate. This section will explore the specific applications of casting molds, focusing on replicating collectible items, creating art pieces, and producing custom jewelry, shedding light on why understanding these applications is essential.
Replicating Collectible Items
When it comes to collecting, rarity can often dictate value. For many enthusiasts, casting molds permit the replication of collectible items without compromising the integrity or quality of the original. Whether it's a rare fossil, a vintage toy, or an intricate figure, having a mold allows collectors to create duplicates that can be displayed or even traded.
- Preservation of Originality: By casting duplicates, collectors can preserve the original item in a safe environment, reducing the risk of damage due to handling or exposure to elements.
- Accessibility to Rarities: Casting molds can help make rare items more accessible. A collector may have a piece that’s one of a kind but using a mold, they can create limited runs for fellow enthusiasts.
- Cost-Effective: Instead of investing in high-priced originals, enthusiasts can create their own copies, allowing them to enjoy their hobby without breaking the bank.
"The art of replicating not only preserves the past but enhances the joy of sharing those intricacies with others."
Creating Art Pieces
Casting molds serve as a fundamental tool for artists wishing to explore three-dimensional creativity. By using molds to cast unique pieces, artists can tap into endless artistic potential, as molds help create consistent replicas of their designs.
- Experimentation with Materials: Artists aren’t limited to one medium. They can create pieces in plaster, resin, or even metal, experimenting with textures and finishes.
- Mass Production: For those wishing to sell their work, molds make it easier to produce multiple copies of a well-received piece, streamlining the process and ensuring consistent quality.
- Unique Designs: Artists can even incorporate unique features into their molds, allowing them to create one-of-a-kind items with distinct characteristics that keep their work fresh and engaging.
Producing Custom Jewelry
The jewelry-making field benefits tremendously from casting molds. Crafters can produce custom pieces tailored to specific designs or collectors’ preferences
- Personalized Pieces: With molds, jewelers can create custom designs that reflect personal narratives or unique styles, enhancing the sentimental value of the pieces.
- Cost Efficiency: Molds can quickly produce intricate designs that might otherwise take a long time to create by hand, saving time and labor costs.
- Rapid Prototyping: Before settling down on the final design, jewelers can make tests and alterations easily using molds, thus refining their works before full production.
Ending
The conclusion of this guide underscores the significance of mastering the art of mold making, particularly for those who are enthusiastic about collectibles and fossil duplication. It isn’t just about having the right techniques; it’s a blend of artistry, precision, and material science that can yield impressive results. Knowing how to craft your own molds can take a collector's practice to entirely new heights, allowing for reproduction of rare finds or the creation of unique artistic pieces.
Recap of Mold Making Essentials
To encapsulate the core ideas discussed in this article:
- Understanding Different Mold Types: Recognizing the difference between rigid and flexible molds is crucial. Rigid molds suit more angular objects, while flexible ones are great for detailed shapes.
- Material Selection: The choice of materials like silicone rubber or plaster of Paris can heavily influence the durability and fidelity of the mold.
- Tools & Setup: Having the right tools and a designated workspace prepared sets the stage for successful mold making.
- Process Flow: From the design of the mold box through to curing processes, each step requires care and attention to detail.
- Troubleshooting: A keen eye for common challenges can save time and materials, particularly bubbles and incomplete molds.
By grasping these essentials, you are positioning yourself to push boundaries in your casting endeavors.
Encouraging Further Exploration
Mold making is an evolving craft, and there is always more to explore. Consider diving into:
- Advanced Techniques: Discover ways to create multi-part molds or lifecasting for more complex projects.
- Workshops & Classes: Local community centers or online platforms may offer workshops that can enhance your skills with hands-on experience.
- Networking with Fellow Collectors: Engaging on forums or groups, such as those on Reddit, can provide insights into different approaches and new materials.
As you embark on (or continue) this journey into mold making, let curiosity guide you. Whether it’s experimenting with new materials or sharing successes and failures with fellow collectors, each step leads to mastery of a craft that marries creativity with technical skill.
"Success is the sum of small efforts, repeated day in and day out."
This could not be truer in the context of mold making; persistence and passion will yield rewarding results.