Mastering the Craft of Stone Polishing Techniques
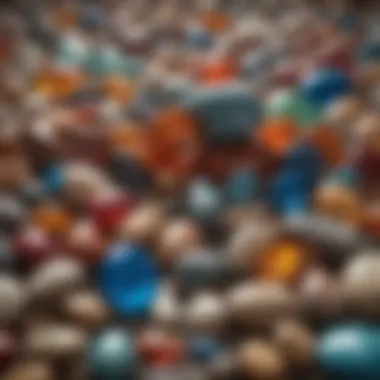
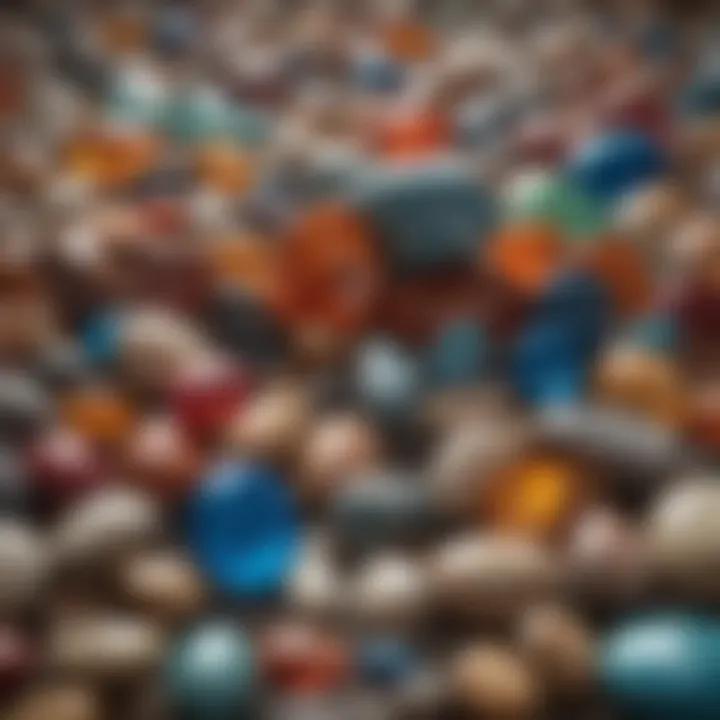
Overview of the Topic
Polishing stones can feel like discovering a hidden treasure; it transforms dull rocks into shimmering gems that catch the eye and spark the imagination. This craft is neither merely a hobby nor just a pastime. It bridges the worlds of art and science, highlights the beauty of nature, and nurtures a profound appreciation for the Earth's bounty.
Definition of Key Terms
To consider the basic tenets of stone polishing, one must understand some terms:
- Polishing: The act of smoothing and shining the surface of a stone.
- Grit: The size of the abrasive particles used in the polishing process. It ranges from coarse to fine, each serving a specific purpose.
- Lustre: This refers to the sheen or glow on the surface of the polished stone, which can vary based on the stone type and polishing technique.
Historical Significance
The practice of polishing stones has deep roots stretching back to ancient civilizations. Cultures such as the Egyptians and Native Americans honed their skills in shaping and finishing stones not just for tools but also for adornments and ceremonial objects. Over time, the techniques evolved, influenced by the availability of tools and abrasives. In modern times, while the science of stone polishing has advanced, the artistry remains a cherished craft, connecting enthusiasts to the age-old traditions of their ancestors.
Types of Collectibles
Understanding the various types of stones one can polish is crucial for collectors. Different stones not only vary in appearance but also in the physical properties that affect how they can be polished.
Classification of Different Collectibles
Stones can be broadly classified into:
- Igneous Rocks: Formed from cooled magma, like granite and basalt, they usually polish well due to their hardness.
- Sedimentary Rocks: These stones, such as limestone and sandstone, can be more challenging to polish due to their layered structure but offer unique patterns when done right.
- Metamorphic Rocks: Examples like marble and slate often have beautiful variances in coloration and texture, making them highly desirable for polishing.
Notable Categories
Polished stones don’t just belong in a case; some can be turned into jewelry, decorative items, or even used in meditation practices. Some notable categories include:
- Cabochons: Smooth, rounded stones often used in jewelry.
- Tumble Stones: Small stones polished in a tumble process, great for collection or decoration.
- Spheres: Polished into a perfect round shape, they symbolize unity and completeness.
"A polished stone is like a canvas for nature's artistry, showcasing the intricate patterns and colors born from millennia of Earth's processes."
Each category possesses unique qualities, reinforcing the importance of selecting the right type of stone for polishing. As one dives deeper into this craft, they’ll discover that the choice of stone directly influences the polishing process, the tools used, and ultimately, the visual impact of the finished product.
Understanding Stone Characteristics
Understanding the characteristics of stones is central to enhancing the art of polishing. Each stone type has unique properties that determine not only its polishability but also the techniques and tools suited for achieving a smooth finish. Familiarizing oneself with these properties can mean the difference between a well-polished stone and a disappointing outcome. It is essential to recognize that not all stones respond the same way to polishing techniques, which highlights the need for a tailored approach.
Basic Mineralogy
To grasp the nuances of stone polishing, diving into basic mineralogy is vital. Mineralogy involves the study of minerals and their properties. Each type of stone, whether it be granite, marble, or sandstone, consists of various minerals that play a role in how the stone can be shaped and polished. Understanding factors like hardness, crystal structure, and chemical composition lays the foundation for making informed choices while selecting stones for polishing.
Types of Stones for Polishing
Polishing stones is not a one-size-fits-all gig. Different stones bring their own characteristics to the table, and knowing the types is like being handed the key to a treasure chest of possibilities. Let’s break down the three main types:
Sedimentary
Sedimentary stones are often layered in their formation. Examples include limestone and sandstone. The key characteristic of sedimentary stones is their relatively soft composition, which generally makes them easier to polish. This can be a benefit for beginners. However, the unique feature of sedimentary stones is that they might have more porous structures. Without proper sealing, they can be prone to staining and erosion over time. Thus, while they are a popular choice for initial projects, it's essential to be mindful of their vulnerabilities.
Igneous
Igneous stones, like granite and basalt, are formed from cooled magma. Their significant aspect is the high density and hardness, which gives them strength and durability. This characteristic makes them a favorite among collectors, as they can achieve a remarkable shine. However, the hardness is a double-edged sword; it requires specialized tools and techniques to polish effectively. Therefore, patience is key when working with igneous stones, as their tough nature can deter those who lack experience.
Metamorphic
Metamorphic stones, such as marble and slate, form under extreme pressure and temperature. Their unique characteristic is the variety of textures and veins that can be beautifully highlighted through polishing. They hold a certain aesthetic appeal that makes them a sought-after choice for both artistic and practical uses. However, the softer areas in metamorphic stones can be more susceptible to scratches. Thus, the polishing process must be approached with care to prevent damage to the intricate patterns.
Identifying Suitable Candidates
When it comes to polishing stones, not every piece hits the mark. It’s crucial to identify suitable candidates which demands an understanding of specific factors that contribute to their polishability.
Hardness Scale
The hardness scale, commonly known as the Mohs scale, is an indispensable tool for identifying suitable stone candidates. Measuring hardness helps to predict how well a stone will respond to polishing techniques. For instance, a diamond scores a 10 on the scale, while talc is at 1. Polishing harder stones like quartz (7) may take additional effort compared to polishing softer stones like calcite (3). Therefore, utilizing the hardness scale allows for informed decisions in selecting the right materials for the polishing process.
Surface Texture
Surface texture of a stone plays a crucial role in determining how effectively it can be polished. A smoother surface often means less resistance during the polishing process. Conversely, rough textures may require more aggressive initial treatments that can lengthen the entire process. Knowing what surface condition a stone is in helps tailor the tactics you use, ensuring that the finished product turns out just right.
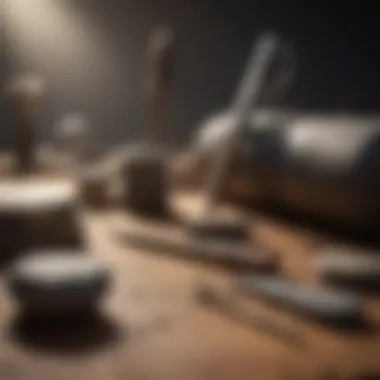
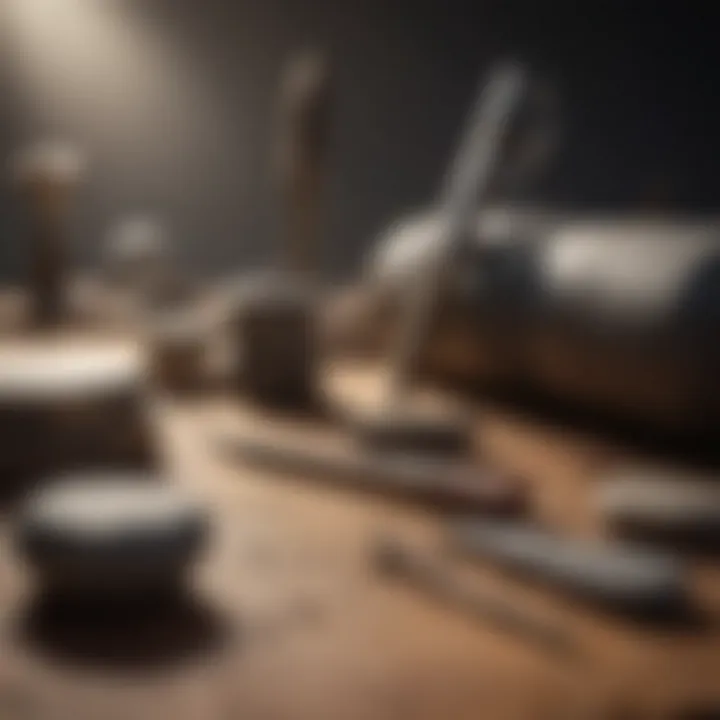
Natural Luster
Natural luster is the way a stone reflects light, which can give you insight into how well a stone might polish up. Some stones, like jade, naturally have a rich luster. Others may appear dull unless properly worked on. A stone's luster can be significantly enhanced with the right polish, showcasing its inherent beauty. Evaluating natural luster at the start assists in setting expectations and preparation steps for achieving that coveted shiny finish.
"When you understand the materials you're working with, you unlock the potential beauty hidden within stone."
Each of these elements forms a building block in the overall process of polishing stones. Understanding stone characteristics equips collectors and enthusiasts with the knowledge to make informed choices and achieve stunning results.
Essential Tools and Materials
Polishing stones requires more than just skill; it calls for the right tools and materials. Each piece of equipment plays a crucial role in refining the surface of the stone, enhancing its natural beauty, and ensuring safety during the process. Without proper tools, one may end up grinding away more than intended or missing the sheen that makes polished stones desirable. Here’s a closer look at the essential components that help craftsmen achieve remarkable results.
Basic Polishing Equipment
Sandpaper
Sandpaper is a fundamental tool in the stone polishing toolkit. This material primarily consists of a paper backing coated with abrasive particles, which facilitates the grinding process. The grit sizes vary from coarse to ultra-fine, allowing for a tailored approach to each project. The key characteristic of sandpaper lies in its versatility—it's suitable for a myriad of stones and offers differing abrasion levels to address various imperfections.
Using sandpaper can provide a controlled method of removing roughness. Its unique feature is its flexibility which allows it to conform to the shape of the stone, making it easier to work on contoured surfaces. However, one downside is that it may wear out quickly, especially on harder materials, potentially requiring frequent changes. Nevertheless, sandpaper remains a popular choice for enthusiasts thanks to its accessibility and effectiveness.
Polishing Wheels
Polishing wheels are another critical element in the stone polishing journey. These rotating tools are usually attached to a bench grinder or a specialized polishing machine and are designed to refine the surface further. The key characteristic of polishing wheels is their ability to cover large surface areas quickly, saving time when working on bigger stones.
These wheels often come in various materials, such as felt or fabric, and can be infused with polishing compounds. A unique feature of polishing wheels is their speed; they provide a consistent finish that hand sanding cannot easily achieve. A potential drawback is that if not monitored closely, they might generate heat, leading to potential damage to delicate stones. Thus, using them requires a careful balance between speed and technique.
Drill Attachments
Drill attachments are perfect for those diving into detailed polishing work. They allow the user to attach various polishing pads directly to their drill, providing a portable and often more convenient polishing solution. One significant aspect of drill attachments is their adaptability; they come in various shapes and sizes, catering to intricate designs or tight spaces.
The uniqueness of these attachments lies in their ability to turn a standard drill into a powerful polishing tool with minimal investment. However, there’s a learning curve; improper use can lead to uneven finishes or even stone cracks if too much pressure is applied. Still, for those adept at wielding a drill, these attachments are invaluable.
Polishing Compounds
Diamond Paste
Diamond paste is a standout among polishing compounds, allowing users to achieve a mirror-like finish on stones. Made with tiny diamond particles suspended in a paste, it effectively smooths surfaces down to a high level of gloss. The main advantage of diamond paste is its effectiveness; it works on even the hardest materials, making it ideal for tough rocks.
Its unique feature is the precision it offers—the small diamond particles have high cutting ability, reducing the number of polishing stages needed. However, this comes at a cost, as diamond paste can be pricier than other compounds, which might deter beginners.
Aluminum Oxide
Aluminum oxide would be another common polishing compound, known for being affordable yet effective. It strikes a good balance between cost and performance, making it a favorite among hobbyists. This compound excels at removing scratches and imperfections efficiently and can be used on various types of stones.
One notable quality of aluminum oxide is its durability; it can be used multiple times which adds to its economical appeal. However, it may not be as effective on harder stones compared to diamond paste, so understanding the stones' hardness is crucial to achieving optimal results.
Rouge
Rouge is often considered the finishing touch in stone polishing. This compound, consisting of iron oxide, is used primarily for polishing metals, but it can also work wonders on certain stone types by bringing out their natural luster. The key characteristic of rouge is its gentleness; it’s perfect for final buffing without risking damage to the stone.
Additionally, its unique feature lies in producing a high shine with minimal pressure required. On the flip side, it may not be effective on all stones, and users should always conduct a test on a small area first. Thus, while rouge is a fantastic choice for that final polish, knowledge of materials is essential for effectiveness.
Safety Gear
Goggles
Safety goggles are a fundamental piece of gear needed when polishing stones. They protect the eyes from dust, debris, and any flying particles that may result from the polishing process. The significance of goggles cannot be understated; they guard against potential injuries that can arise unexpectedly while handling various tools.
The beauty of modern safety goggles is that they are generally lightweight and comfortable, allowing long periods of wear without discomfort. However, users must ensure that the goggles fit securely to gain the utmost protection.
Respirators
Respirators are vital when working with certain polishing compounds, as they filter out harmful particles and fumes. The importance of wearing respirators cannot be emphasized enough—breathing in fine dust or chemicals can lead to long-term health issues.
One key highlight of a quality respirator is its filtration efficiency, with many offering various levels of protection. Still, users should be cautious about finding the right fit; a poor-fitting respirator is less effective and can cause irritation.
Gloves
Protection for the hands is equally crucial, making gloves an essential part of the polishing process. They provide a barrier between the skin and abrasive materials or chemicals, preventing cuts and irritation. High-quality gloves can offer excellent grip, ensuring that tools are handled safely and effectively.
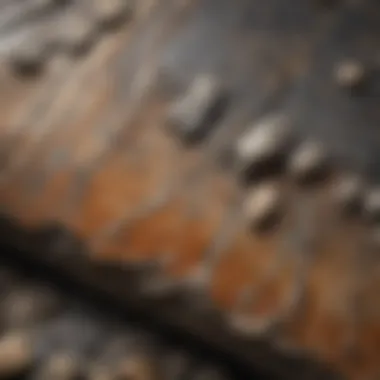
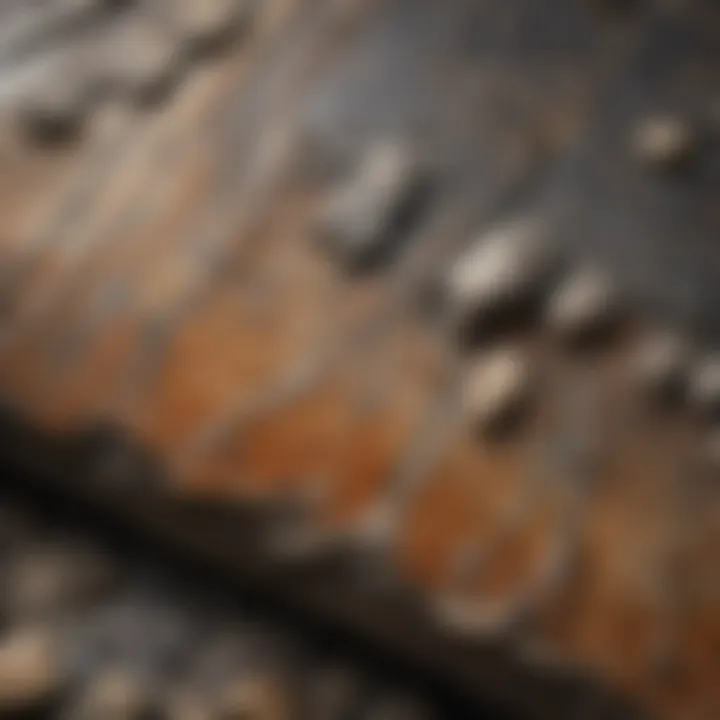
The unique feature of gloves lies in their variety, allowing users to select material types based on the specific task at hand—rubber for wet work or fabric for general handling. However, it's wise to check for punctures or tears regularly, as damaged gloves provide insufficient protection. Overall, while gloves may feel optional, they contribute significantly to safety and comfort during stone polishing.
Initial Preparation of Stones
Getting the stones ready for polishing is a crucial step that shouldn’t be brushed aside. This initial preparation sets the stage for the entire process, acting as the backbone for any future success in achieving a sleek, beautiful surface. When you take the time to thoroughly prepare your stones, you minimize potential hiccups down the line, resulting in a polished finish that you can truly appreciate. Think of this phase as the prelude to a symphony; without the right notes introduced early on, the final performance is unlikely to impress.
Cleaning the Stones
Using Water
Water is one of the most straightforward and accessible cleaning agents. It's often the first course of action when dealing with dirt and grime on stones. You just rinse or soak the stones, and they come up looking fresh and earthy. The main characteristic of using water is its gentleness on the stones; it’s a nurturing option that doesn’t risk damaging any surface features. A beneficial aspect of water is that it washes away loose dirt and debris effectively without introducing harsh chemicals into the mix. If you rely solely on water, be mindful of how you dry the stones afterward; air drying may create mineral deposits that could affect the finish.
Chemical Cleaners
Chemical cleaners offer a more robust option for cleaning stones, particularly when confronting stubborn stains or residues that water alone can’t handle. These products often contain specific compounds designed to break down tough dirt, making them a popular choice among polishing enthusiasts. The key characteristic here is their potency—in many cases, they’re more efficient than traditional methods. However, here’s the catch: some chemical cleaners can be harsh and might damage softer stones or alter their color. So, a careful read of instructions and understanding the stone type is highly important for those considering this route.
Ultrasonic Cleaners
Ultrasonic cleaners are a state-of-the-art option that many collectors may consider an investment, although their effectiveness can be well worth the cost. These devices use high-frequency sound waves in a liquid solution to disrupt dirt particles on a stone’s surface, thereby achieving a thorough clean without abrasive contact. A major benefit of ultrasonic cleaners is their ability to get into intricate details that brushes or cloths might miss. While they come with a high price tag and require some technical know-how to operate, the results can be astonishing, leaving stones looking perhaps better than they have in years.
Assessing Imperfections
Evaluating Chips
Before diving right into polishing, evaluating any chips on your stones becomes paramount. It’s about taking a good look at what you have and understanding the starting point. Chips can limit how effective your polishing will be because they may lead to uneven surfaces or not enough material to work with. One key characteristic of this evaluation process is that it requires a keen eye for detail. This assessment thus becomes a popular choice early in the polishing process, as it's essential to acknowledge all imperfections first. A downside, however, is the possibility that some chips might require you to alter your approach or choose specific grit more cautiously should they be a concern.
Identifying Cracks
Identifying cracks is another necessary task in the initial preparation of stones. Cracks can dictate how and if a stone can be polished at all. This evaluation not only affects the aesthetic quality post-polish but can also influence the durability of your work. Finding these flaws early on allows the polishing process to be adapted accordingly. A key trait of recognizing cracks is that it involves both visual inspection and, at times, a tactile examination. Unfortunately, the presence of cracks can severely limit the final polishing outcome, necessitating caution and sometimes rejection of the stone.
Determining Depth of Flaws
Understanding the depth of any flaws is often overlooked yet is essential in selecting the right polishing method. This step can clarify just how much work needs to be done and help you choose the right tools and techniques later on. Knowing the depth helps in preventing polishing too quickly or too deeply, which can lead to further damage. It's a vital checking point that merits serious consideration. However, one disadvantage is that deep flaws may require professional-grade tools and experience to handle correctly.
Choosing the Right Grit
Understanding Grit Numbers
When it comes to polishing, understanding grit numbers is like knowing the playbook—it helps you pick the right sequence and tools necessary for your desired outcome. Each grit number corresponds to the coarseness of the sandpaper or pad; lower numbers mean rougher surfaces, while higher numbers indicate finer finishes. The benefit of grasping this concept is that it allows collectors to tackle a range of surfaces effectively and purposefully. It’s relatively straightforward to learn but can be nuanced in practice. Yet, choosing the wrong grit can lead to an uneven finish or even damage if one jumps ahead too quickly.
Progressive Sanding Techniques
Progressive sanding techniques are an effective approach to gradually refine the surface of your stones. This method involves starting with a coarse grit and moving to finer grits in stages. One of the main things that make this technique appealing is that it allows for greater control over the polishing process and often yields a smoother finish by the end. However, it can be time-consuming and requires patience. Failure to adhere to this gradual approach can result in scratches or an unsatisfactory finish.
Tools For Different Grit Levels
Using specific tools for various grit levels makes a significant difference in efficiency and effectiveness. For instance, some collecters may opt for sponge-like pads with finer grits for later stages to produce that sought-after glassy finish. The unique feature of having the right tools at your disposal ensures you won’t waste time or damage your stones unnecessarily. While investing in multiple types of tools can mean a considerable upfront cost, collectors often find their value evident through superior results in the long run.
The Polishing Process
The polishing process is central to transforming rough stones into stunning pieces that reveal their inner glory. It’s not just about making stones shiny; it’s about enhancing their natural beauty and preserving their structural integrity. Effective polishing can breathe life into stones such as quartz, agate, and jasper, showcasing colors and patterns that may have otherwise gone unnoticed. Through each step of polishing, from initial shaping to final finishes, one gains the satisfaction of crafting something beautiful and personal.
Initial Shaping
Shaping with Coarse Grit
When starting the polishing journey, using a coarse grit is like laying the first stroke on a blank canvas. This stage is crucial for removing rough patches and imperfections that could mar the eventual finish. Coarse grit, often ranging from 60 to 120 grit, is designed to swiftly reshape and refine stones. One of the standout characteristics of this grit is its aggressiveness; it significantly brings down the high spots, allowing for a smoother surface to work on later. This makes it a popular choice for beginners, as it builds confidence by showing quick results. However, achieving too much pressure or staying too long with coarse grit can cause unwanted scratches, which leads to extra work later down the line.
Achieving Basic Contours
Once the initial shaping is done, the next step—achieving basic contours—focuses on refining those shapes into smoother, flowing forms. This stage is where the stone begins to take on its final shape, revealing its potential beauty. The process often involves transitioning to medium grits, usually ranging from 220 to 400. A significant aspect here is that it allows the craftsman to accentuate the stone’s natural lines and curves. This step is beneficial, as it prepares the stone for the finer polishing stages. While it offers fantastic opportunities for creativity, caution must be taken to avoid removing more material than intended, which could lead to a loss of unique characteristics.
Working on Flat Surfaces
When polishing flat surfaces, one can focus more on precision. Flat stones, like slabs, require careful attention because their appeal often lies in their even surfaces. Typically, this involves using a flat lap machine or dedicated hand tools. The key characteristic here is the uniformity of the surface; achieving a flat polish enhances the stone’s visual allure. This method is often favored by gem cutters and collectors looking to create refined displays. One downside, however, is that it can become tedious if not planned or executed carefully, as maintaining pressure evenly can be tricky. Missing any spots means having to redo parts of the work, which can eat into project time.
Progressive Polishing
Shifting from Coarse to Fine Grit
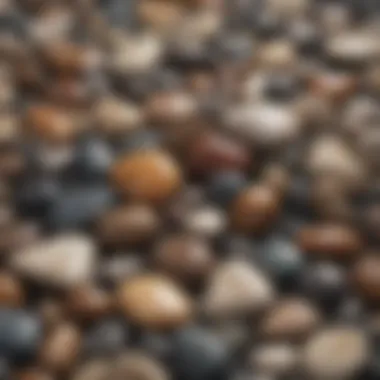
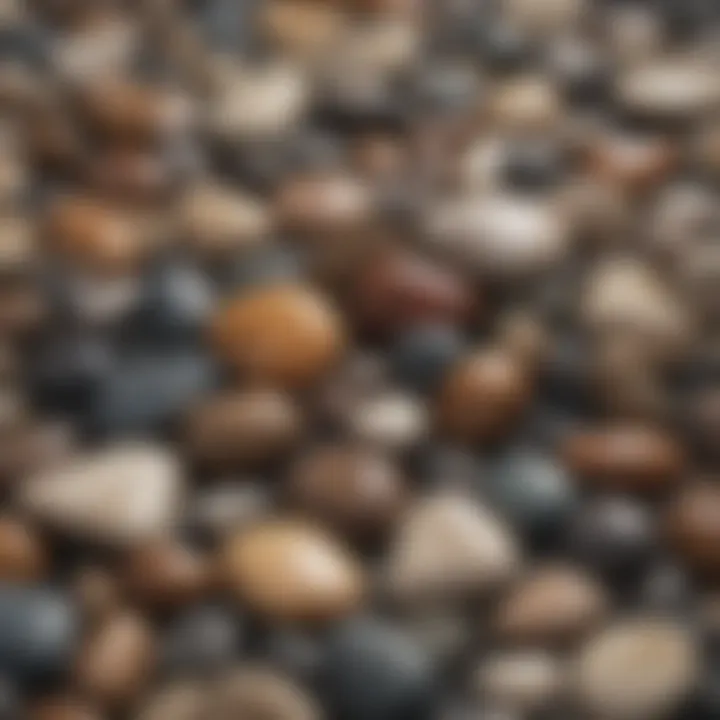
Shifting from coarse to fine grit is a pivotal moment in the polishing journey. This transformation reflects the transition from structure to beauty. Fine grits, ranging from 600 to 3000 and beyond, allow for a more delicate approach, smoothing out the surface achieved from coarser levels. The key characteristic of this stage is the attention to detail it demands; where coarse grit is about shaping, fine grit is about finesse. It’s a beneficial choice as it lays the groundwork for the brilliant finish that’s to come. However, it requires patience and precision, as skipping back to coarser grits prematurely can ruin the progress.
Technique for Smoothness
The technique for achieving smoothness is closely tied to the individual's method and choice of tools. Utilizing polishing pads or cloths with fine compounds allows for a refined surface that catches the light beautifully. This is where artistry comes into play—the varying angles and pressures can all result in unique patterns on the stone’s surface. While it is a favored technique for many, mistakes can be costly; a misstep here can set you back hours. Moreover, the potential for creating uneven spots necessitates careful monitoring of the entire surface throughout the process.
Polishing on a Wheel
Polishing on a wheel is a time-honored method that offers efficiency and consistency in achieving the desired sheen. The circular motion of a polishing wheel allows for even pressure across the stone, which is critical for maintaining uniformity. It’s popular among professionals due to its speed and effectiveness. One unique feature of this method is its adaptability; different wheels can be used for different stone types and desired finishes. However, it does require skill to manage properly, as improper use can lead to overheating, compromising the stone’s integrity.
Final Finishes
Applying Polishing Compounds
When it comes to the final stages, applying polishing compounds is like adding the final brush strokes to a masterpiece. These compounds, often made from ceramics or diamonds, enhance the stone's shine significantly. The key characteristic of this stage is the transformation—from just a polished stone to one that sparkles with life. It’s an essential part of the process, ensuring a finish that not only looks good but also feels smooth to the touch. Though it is highly effective, applying too much compound can leave a residue that needs further cleaning, so a light touch is advisable.
Buffing Techniques
Buffing techniques can elevate the polishing results into the realm of the extraordinary. This process, using soft materials or wool, creates a lustrous glow that is often associated with high-end gems. A crucial aspect of buffing is the combination of speed and friction; finding the right balance can make all the difference in the final appearance. Many collectors see buffing as an art form in its own right, as different techniques can yield varying results on the same stone. While effective, excessive buffing can wear down the delicate features of some stones, necessitating a nimble approach.
Quality Control Check
Quality control is often the last line of defense against imperfections. This step involves a thorough inspection of the polished stone, checking for consistent shine and minor defects. The key characteristic is that it allows for the assessment of the overall quality, ensuring the stone meets both aesthetic and structural standards. It’s a beneficial choice for serious collectors who are invested in their pieces' values. One has to be careful, though, because overlooking small flaws can undermine the entire polishing effort.
Maintaining Polished Stones
Maintaining polished stones is often the unsung hero of stone collecting. Once you've invested the time and effort into achieving that lovely luster, it only makes sense to put a little elbow grease into keeping it that way. This section delves into critical aspects of maintenance, focusing on strategies that ensure your hard work pays off long-term. By following these guidelines, collectors not only preserve their prized possessions but also enhance their natural beauty for years to come.
Storage Considerations
Storing polished stones with care is essential for maintaining their aesthetics and integrity. Improper storage can lead to scratches and deterioration, which can be heartbreaking for any enthusiast.
Avoiding Scratches
Avoiding scratches is paramount when storing polished stones. Scratches can ruin the surface and dull the shine, making your stones look worn out and tired. The key characteristic of this practice is the careful arrangement of your collection. By using padded containers, like soft fabric bags or foam-lined boxes, you eliminate the risk of contact with other stones or objects. This practice stands out not just for its effectiveness but also as a gentle reminder to treat these pieces of nature with respect. The unique feature of focusing on avoiding scratches is its simplicity; a little planning goes a long way. It’s a beneficial choice that provides peace of mind, knowing your stones are safe from unforeseen damage.
Humidity Control
Humidity control plays a significant role in preserving polished stones. An environment that's too moist can promote mold growth or cause fast deterioration of certain minerals. The key characteristic here is the equilibrium—maintaining just the right moisture level. By storing stones in a climate-controlled area, it's easier to avoid the pitfalls that come with excessive humidity, such as tarnishing and degradation. This method proves to be advantageous since it not only protects the stones but also prolongs their life. The unique feature of humidity control is that it keeps your collection not just looking good, but also in a condition where it remains safe for display and enjoyment.
Displaying Your Collection
Displaying your collection properly can enhance your home and bring attention to the beauty of each piece. The appeal of well-displayed stones is their ability to captivate and charm viewers. A main characteristic to consider when exhibiting stones is the use of display cases that allow for dust-free environments. This displays their natural sparkle without risking wear and tear from exposure. Setting up showcases makes the collection more than just a hobby; it turns it into a visual narrative. A unique aspect of showcasing your collection is the way it invites conversation—friends and fellow collectors will admire your taste and possibly seek your advice on their own collections. However, while it can be rewarding, it’s imperative to be mindful of sunlight exposure, as too much direct light can harm certain types of minerals over time.
Cleaning and Care
Regular cleaning and upkeep ensure that your polished stones retain their initial brilliance. The focus on cleaning and care highlights a commitment to maintaining the craftsmanship involved in polishing these pieces.
Regular Maintenance
Regular maintenance is the backbone of stone care and should become a routine practice. It involves dusting and light cleaning as the mainstay of the process. Keeping stones dust-free not only maintains their shine but also prevents the buildup of grime that can lead to scratches. The key takeaway is that a little bit of loving attention goes a long way; dusting every couple of weeks is a manageable task for any collector. Its significant benefit is the preventative measure it offers against more daunting tasks later on. The unique aspect of routine maintenance is that it is flexible. Whether you are a meticulous or a more laid-back collector, there’s no one-size-fits-all in this practice.
Safe Cleaning Products
Using safe cleaning products is essential to ensuring that your stones survive the care process. Abrasive substances can cause more harm than good, dulling their surface or even promoting scratches. The distinguishing characteristic of safe cleaning products is their gentle, non-abrasive nature, as well as their efficacy. Opting for solutions that pose no risk ensures that you can regularly clean without worry. This choice is particularly favored as it maintains both aesthetic appeal and integrity of the stones. The unique feature of focusing on safe cleaning is the broad spectrum—many household products are suitable for this purpose, which reduces costs while providing reliable care.
Routine Inspection
Routine inspection can be the unsung hero in the care of polished stones. By regularly checking for imperfections or hidden damage, collectors can address issues promptly. The primary characteristic of routine checks is their proactive nature. Keeping an eye on each piece helps catch potential problems before they escalate into something more severe. This might seem tedious, but the benefits far outweigh the minor inconvenience. By adjusting inspections to align with the overall storage and cleaning routines, collectors can develop a strategy for consistent care. The unique aspect of this practice lies in the relationship it fosters with the collection—being familiar with each piece enhances appreciation and understanding of their unique qualities.
Common Issues and Solutions
Despite the best efforts at maintenance, challenges can arise in maintaining polished stones. This section explores effective strategies for addressing common issues that may surface over time.
Restoring Faded Polishing
Restoring faded polishing is often necessary, especially for stones that have been displayed prominently. Over time, exposure to elements can dull the sheen that once captivated. The key feature of this process is utilizing polishing compounds effectively, allowing for the restoration of lost luster. This practice is generally popular among collectors who desire longevity and brilliance in their displays. The unique aspect is that various methods can be applied, from simple buffing to using chemical compounds designed specifically for restoration. While this solution can be rewarding, it’s crucial to approach it with caution—some stones are more sensitive than others.
Repairing Minor Scratches
Repairing minor scratches can feel like a daunting task, but it's often simpler than anticipated. The main characteristic of this process is its accessibility; supplies for minor scratch repair are typically easy to find. Simple tools like a soft cloth and fine polishing compound can do wonders in restoring the surface. This practice is beneficial because it allows collectors to maintain their items themselves, skipping the need for professional repairs. The unique feature here is that many tricks are available to achieve a commendable shine, thus empowering collectors to take charge of their beloved stones.
Dealing with Chemical Damage
Dealing with chemical damage can stem from exposure to harsh cleaning products or environmental factors. Understanding what types of chemicals can affect polished stones is key to preventing future issues. The characteristic of this issue often involves identifying specific sources of damage, which allows for effective remediation. This practice is particularly relevant for intensive collectors who may use various products in their care routines. The unique element of navigating chemical damage is the need for education; knowing what to avoid can help protect a collection from similar fate. While addressing damage can be challenging, it's crucial to approach it with an informed perspective, ensuring the best possible outcomes for your stones.
Keep your collection not just beautiful, but in the best condition possible. Investing time into maintenance today pays dividends in the future.